Feedback |
|
Find: | |
- The following are Letters to the Editor and Feedback entries we have received as a result of our editorial content and weekly Alert Editor's Desk Comments. To Have your say on industry news and developments, Signup to our free weekly Alert and be updated on the world's tunnelling news and views.
Advice following stacked drift experience
-
Article referenceStacked drifts as presupport– TunnelTalk April 2021
- Feedback from: Victor Romero, McMillen Jacobs Associates
- Dear Editor,
- I read with great interest the April 2021 article on Stacked drifts as presupport. It is a nice summary and brought back a lot of memories as engineer of record for the Rio Piedras Station in Puerto Rico - some good, some not so good.
- The good memories were all the great people I worked with at Kiewit, Soletanche, McMillen Jacobs and the owner, past and present, because it was a huge, challenging effort to implement the design and construction, and we were using the emerging technology of the late 1990s of compensation grouting, with real time settlement monitoring.
- The not so good memories were mainly the poor ground, low cover conditions and leaking utilities that we faced. But we got there in the end.
- One thing the article did not mention was there was another stacked drift going on at the same time for the underpinning of South Station on the Big Dig underground highway project in Boston. The project faced significant challenges there as well, but not as much was published, unfortunately, and there are other examples of application of the technique in Italy, I believe.
- I occasionally get asked about the stacked drift method on some projects when in planning stage. Of course each project is different with respect to ground conditions, site constraints, and functionality of the finished structure, so sometimes, in very rare circumstances, a stacked drift may be a viable solution. But it is slow and costly, and new technologies mean we have other options to consider for very large diameter excavations.
- In many cases SEM/NATM is viable, although application of many additional control measures in the toolbox may be needed. Settlement mitigation and monitoring measures have greatly improved. For longer tunnels, TBM segmentally lined excavations are pushing some amazing diameters now.
- While I am happy to see others might be attempting the stacked drift method, my advice is to proceed with caution and make sure your design and construction methods are fully integrated. Yes, that is true for any tunnel project, but especially so when building a stacked drift project.
- Regards,
Victor Romero, PE CPEng,
President - Underground Division,
McMillen Jacobs Associates
Highway tunnel box jacking in Boston, USA – TunnelTalk April 1997
Exploring critical elements for NATM success – TunnelTalk June 1995
Rekindled NATM debate - SCL debate opens – TunnelTalk August 2012
Beware repeat project optimism
-
Article referenceRepeat operation for Nepal second TBM drive – TunnelTalk April 2021
- Feedback from: Siba Prasad Sen, Independent Consultant, India
- Dear TunnelTalk,
- It is very unlikely that the Sunkoshi Marin TBM diversion project in Nepal will be a repeat of the Bheri Babai TBM experience, due mainly to the expected presence of high pressure water ingress and distressed rock. Also, I do not think that your suggestion of provision of a contingency fund can alone take care of such risks in absence of advance planning.
- While assisting in the preparation of the feasibility report for the Bheri Babai multipurpose project and in association with Nepal irrigation engineers, two things were in mind: First, it was to be the first TBM project in Nepal, and secondly we did not know whether there was a good probability of presence of ground water in high pressure and high volume in the form of either or both perched or pressurised aquifers. Investigation study data, drill hole information and a walk over the Bheri Babai alignment did not indicate that high-pressure, high-volume water issues would be so.
- It has been the general experience that the presence of water in high pressure along an alignment has been a recipe for disaster, especially for excavation by TBMs in the Himalayas. The Dulhasti and Parbati II projects are examples. The current Tapovan and Vishnugad hydro projects have also experienced the presence of high-pressure ground water.
- With limited information on geology and geotechnical data being available for the Tapovan Vishnugad project I understand that the alignment had some kind of syncline rock strata, which should have been taken as a red signal for ground water. It is true that further development of geological and hydrological investigation methodology in the Himalayas is required, as suggested by Rupert Sternath in his Feedback contribution.
- In the Himalayas, the presence of substantive water can change the engineering behaviour of rock. I am not sure whether high-pressure ground water is accounted for while designing the TBM and planning for the excavation of projects in the Himalayas. Many owners and contractors use the excuses of difficulty in conducting site investigations and lack of sufficient experience of the complexities to start the work in a hurry and without doing any investigation at all.
- In case of Bheri Babai in Nepal and the Kishanganga hydro scheme in India, the presence of water was not high, though the geology was as complex as it has been on other projects.
- For the proposed Sunkoshi Marine project in Nepal, Shani Wallis of TunnelTalk wrote an excellent report on the proposed project in September 2020. Though brief, it gives a good idea of the complex geology of the project. The most important point is that the alignment crosses the Main Boundary Thrust of the Himalaya Massif and that it has to pierce through the major syncline of the Nepal Himalayas. Experience confirms that such a syncline willl have high stress and the presence of quartzite bands and must also anticipate to have the presence of high pressure and high volume ground water.
- As I am not aware of the detailed geology and investigation data of the Sunkoshi Marine project, I can only say that in planning the TBM technical specification and the excavation processes, provision should be made for large quantities of water flow. It may be advisable to try some investigation for the presence of high pressure, high volume water along the tunnel path.
- Sincerely,
Siba Prasad Sen,
Independent Consultant,
New Delhi
Quantifying reliability in geological prediction– TunnelTalk March 2021
Nepal preparing for second TBM project– TunnelTalk September 2020
Nepal proving TBM applicability in Himalayas – TunnelTalk February 2019
TBM rescue for Tapovan hydro challenge – TunnelTalk December 2016
Vishnugad Pipalkoti TBM finally set to start– TunnelTalk October 2019
New award follows Seli Kishanganga success (with video) – TunnelTalk May 2014
Breaking excavation records in the Himalayas – TunnelTalk December 2012
Claimed as the most difficult TBM project ever– TunnelTalk April 2021
Learning from difficult rock TBM drive experiences– TunnelTalk January 2021
Geotechnical descriptions in tender documents
-
Article referenceNepal preparing for second TBM project – TunnelTalk September 2020
TBM rescue for Tapovan hydro challenge– TunnelTalk December 2016 - Feedback from: Rupert Sternath, Germany
- When I read recently the remarks on geotechnical descriptions in the tender documents in the TunnelTalk article about a second TBM waterway tunnel for the Sunkoshi-Marin Project in Nepal, my first thought was to recall the headrace tunnel for the Tapovan Vishnugad hydroelectric project in the Himalayas. I did not experience in my more than 40-year tunnelling career a greater difference between the descriptions in the tender documents and the reality met in the tunnel.
- In accordance to the tender documents, the contractor chose a double shielded TBM with a reasonable conicity to overcome rock movement due to plasticity effects of the weak rock conditions in the mountain. The result of these facts is that different contractors are now struggling with the conditions, with the TBM becoming jammed repeatedly since 2007.
- In 2016 I read in TunnelTalk the optimistic report on the TBM recovery there by a new start. But even the new contractor, who could master the tremendously difficult conditions on the Kishanganga headrace tunnel near Srinagar in Kashmir, also got stuck with the TBM there several times.
- I wish the current contractor wholeheartedly all necessary understanding and support by the client NTPC, enabling it to adjust the tunnelling methods to these really unexpected conditions. Further reports in TunnelTalk on this very interesting project would be very much appreciated as the tunnelling community could learn a great lecture out of this!
- Sincerely,
Rupert Sternath,
Tunnelling Engineer,
Germany - From the Editor: Thank you Eng Sternath for the Feedback and suggestion. TunnelTalk has been following the development of TBM water tunnel projects in the Himalayas over the years, as well as in difficult high overburden mountain conditions for projects elsewhere in the world, and will work on an update article about the experiences on the Tapovan Vishnugad project for publication in the coming weeks.
Hydropower watercourse failures - risks and causes – TunnelTalk March 2020
Hydro TBM risk assessment and selection – TunnelTalk March 2020
Vishnugad Pipalkoti TBM finally set to start – TunnelTalk October 2019
World Bank backs Vishnugad Pipalkoti hydro – TunnelTalk July 2011
New award follows Seli Kishanganga success – TunnelTalk May 2014
Breaking excavation records at Kishanganga in the Himalayas – TunnelTalk December 2012
VIDEO: Kishanganga hydro headrace TBM drive success in the Himalayas – TunnelTalk 2012
Search
Awareness of the threat of glacial lake outburst floods
-
Article referenceFatal flood hits hydro works in the Himalayas - TunnelTalk February 2021
- Feedback from: Dr Gyanendra Lal Shrestha, Nepal
- It was with great concern and distress that we learned of the expected glacial activity deluge that hit the Alaknanda and Dhauliganga River valleys in the Himalayas in India, and of the devastation, damage and deaths that it caused in the villages and to the dams and tunnels at the hydropower plants and construction sites.
- Glacial lake outburst floods have been a clear and present danger in the countries of the Himalayas where glaciers and glacial lakes are also major sources of freshwater. It is known that the cryosphere in the Himalayas is vulnerable to global climate change and glaciers have been melting at an unprecedented rate since the mid-20th century. This leads to expansion of existing glacial lakes, formation of new lakes, and an increase in the risk of glacial lake outburst floods. Nepal has experienced several such outburst floods in recent decades.
- A 2011 study by the ICIMOD International Centre for Integrated Mountain Development of theUnited Nations Development Programme (UNDP) reported 24 glacial lake outburst flood events in the past in Nepal, 14 of which had occurred in Nepal, while 10 were caused by overspills due to flood surges across the border between Nepal and the Tibet autonomous region of China. Most of them caused human and economic losses.
- In 2015, the ICIMOD, based in Nepal and funded by the Government of Norway and the Swiss Agency for Development and Cooperation (SDC), began a study of the threat of glacial lake outburst floods (GLOF) in the Koshi, Gandaki, and Karnali River basins. The study report, published in late 2020, and found that there are 47 potentially dangerous glacial lakes in these basins. Of these, 21 are located in Nepal, 25 in the Tibet autonomous region of China, and 1 in India. A pdf copy of the report is attached for study.
- The water levels of four lakes, two in Nepal and two in the Tibet autonomous region of China, had been lowered in the past to reduce the risk. The water level of Tsho Rolpa Lake in the Rolwaling Valley in Nepal was lowered by more than 3m in 2000, and in 2016 the level of the Imja Tsho Lake in Nepal was lowered by 3.4m.
- Since the late 1980s, we have been including a GLOF study report in most of the snow-fed hydro projects under development and feasibility study in Nepal. The recent incident in Uttarakhhand in the Himalayas in India has further alarmed us.
- Sincerely,
Dr Gyanendra Lal Shrestha
Chartered Engineer, MICE
President - Nepal Tunnelling Association - Download a copy of the 2020 ICIMOD report
Swiss glacier drainage tunnel in full flow– TunnelTalk April 2010
Glacier tunnel protects Swiss communities– TunnelTalk November 2009
Global review of hydropower developments – TunnelTalk March 2020
Nepal harnessing the power of the Himalayas – TunnelTalk April 2020
Geological modelling to aid real site investigation studies
Feb 2021
-
Article referenceLearning from difficult rock TBM drive experiences– TunnelTalk January 2021
Editor's Desk comment – TunnelTalk Alert, 28 January 2021
- Geotechnical reports are an important part of TBM specification and success but are no substitute for real site investigation and understanding. Finding the sweet spot between geological modelling and understanding actual ground conditions and behaviour is the challenge.
- Feedback from: David Fawcett
- Dear TunnelTalk,
- As a given, geotechnical reports should be the result of real site investigation and understanding. This is the fundamental basis of any tunnelling project.
- With regard to geological modelling this should be used in the first instance to assist in specifying the initial site investigation. It is in no way any alternative to physical site investigation. Site investigation is an iterative process that should be designed by a suitably qualified and knowledgeable geotechnical engineer.
- Determining the necessary detail to enable TBMs to be appropriately specified, and their likely behaviour in the ground to be understood, is an issue. Each type of TBM and each manufacturer will have differing parameters that are used to design machines. Each type of machine will have differing ground behaviour parameters that are important to its successful operation.
- Thus, the whole process remains iterative and interactive until the machines have been designed and the operators have fully understood how to use them successfully.
- There is no substitute for a knowledgeable geotechnical team leading, and remaining involved, in the site investigation and geotechnical reporting process from project conception through to successful tunnel completion.
- Geological modelling can only be the first step in this complex process.
- Geological modelling can however be used to assist in predicting likely and /or possible ground conditions in instances where physical site investigation is not practical, for example in high mountain environments. In such situations the modelling must carry a health warning and the chosen TBM must be versatile enough to overcome a much wider variety of ground conditions than when real information is available.
- Best regards,
David Fawcett
Tunnelling Consultant
Past Chair of the BTS, British Tunnelling Society, 1995-1997
Keep your TBM moving against the odds TunnelTalk – TunnelTalk June 2017
Clawing success from the extreme at Arrowhead TunnelTalk – TunnelTalk December 2007
Delusional expectations for predictably difficult TBM drives
Feb 2021
-
Article referenceLearning from difficult rock TBM drive experiences – TunnelTalk January 2021
- Feedback from: Dr Nick Barton
- Dear TunnelTalk,
- The lessons by Lok Home are nice to see. Such things, particularly geologically focused delays, have been the objective of the Qtbm model for the last 20 years, with, unlike many other methods, a specific expectation of a tunnel-length dependent utilization – because that is what the case records have been telling us for a long time. This is the case also with double-shield TBMs, though with greater efficiencies and less delays in general.
- It has therefore been encouraging to see the gradually increasing number of pre-injection ports on shield TBMs in addition to improved probe-drilling facilities over recent decades, a lot led by Robbins and on Herrenknecht and other TBM manufacturers machines as well.
- We have to be prepared for many eventualities. For example, the mean PR (penetration rate) for 36km of recent TBM excavation projects has been close to 2m/hr due to the hard and quite massive rock, while the mean AR (advance rate) taking all time into account, including pre-injection needs and as an end of project mean for a 36km total, has been 500mm/hr. This is due to deceleration with time over tunnel length (Figs 1 and 2). The declining lines are based on open-gripper case records(1), but the TBM world records (held mostly by Robbins TBMs) follow similar trends. It is recognised that a very efficient double-shield operation may have half the deceleration gradient of that of an open-gripper TBM.
- Barton, N. 2000. TBM tunnelling in jointed and faulted rock. 173p. Balkema, Rotterdam.
- Barton, N. 2013. TBM prognoses for open-gripper and double-shield machines: challenges and solutions for weakness zones and water. Fjellsprengningsteknikk, Bergmekanikk, Geoteknikk, Oslo, 21.1-21.17, Nov. 2013.
- Feedback from: Dr Trevor Carter
- It was excellent to hear Lok Home give such a frank presentation of ground control difficulties experienced in the three challenging Robbins rock TBM projects he discussed in the BTS meeting. As he stated, this sort of detail is seldom publicised even though many are aware of these types of situation not being uncommon.
- The comments he made about prediction inaccuracy of technical bid documents (only 40% accurate in one case) resonate with a theme of increasingly delusional expectations that seem to be prevailing across the industry. The delusion is that fancy geological computer models are necessarily reliable, and worse still that they constitute an adequate substitute for real site investigation data and understanding. The delusion abounds to the extent that all too often wishful thinking geology results in poor TBM designs! Unfortunately, in many cases, when this is found out, it is months after the TBM has been built and when it is now deep under the mountains. Lok’s comments that equipping machines with gear for better forward probing and a need for more mapping in every type of tunnel are spot on, but these techniques are directed only at providing data to help negotiate the now identified problems, but after the fact. By this time the TBM is already built, starting maybe 18 months earlier, based on perhaps erroneous geology data and often based on a far too optimistic or unreliable GBR.
- That is where I see the real problem lies – getting better geological and geotechnical understanding into early stages of projects, so that, rather than having to try to retrofit an already built machine to cope with ground conditions that might have been an expected possibility, the necessary capabilities are built into the machine design right from square one.
-
Fig 1. Searching for the sweet spot between how much needs to be known and site investigation investment(1)
- Yet again we heard this message from Lok, but this is part of the delusion and applies also to other major parts of a project. This is an old message that seems to be increasingly ignored. My perception is that with increasingly analytical sophistication in geotechnical engineering and enhanced 3D geological modelling and visualization as part of design interpretation, matters concerning understanding actual ground conditions and behaviour (which should be what controls the design and specification for the TBMs according to the ground prediction reports) is getting worse, not better. There is a worrying trend prevalent industry-wide of the increasing use of more and more modelling tools based on less and less real data. This trend towards generating pretty models (with miserable data) is leading to an increasing lack of real understanding. However, the parallel trend to production of GBRs (geotechnical baseline reports) on all projects, while applauded, must be tempered by the fact, as Lok also alluded to, that many are unrealistic, either biased and optimistic at one extreme or too risk averse at the other. Preparation of GBRs that lack a firm factual foundation that provides some bracketing to hard data are merely adding to a delusion of improved risk management, when in fact the reverse is the reality. Risk registers are only part of the answer. Education to counter the delusion that current state-of-practise leads to is the other part of the equation.
- As an aid to addressing this worrying trend to delusion through visually impressive modelling, I have upgraded my 1992 risk diagram (Fig 1) to help address three key questions:
- How much understanding at any geological complexity level is needed;
- How much investigation to achieve that understanding is enough; and
- If a given amount of money is spent on geological investigation, can this realistically reduce the risks so well illustrated in Lok’s presentation.
- The updated graph (which draws on more recent publications relating to better assessing geological reliability for tunnelling(2,3)), puts into perspective real underground risk versus perceived risk, with data benchmarked to real levels of understanding based on:
- How much is a project willing to spend on site investigation;
- How much is known about the complexity of the geology; and
- The reality of diminishing returns of more extensive site investigation in more complex geology.
- Obviously, there is a sweet spot on all projects for deciding how much needs to be known. After that, more expenditure is counterproductive, but below which, too little hard data is dangerous.
- On the basis of pay now or pay later, up front expenditure is always better than the reality of downstream claims and remedial works costs. However, nowadays there seems even more reluctance to spend money on upfront site investigation. Hopefully, the graph in Fig 1 can prompt deeper thinking about this. Perhaps at least it can provide some guidelines that project planners can use to start to define how much needs to be spent to adequately de-risk a project, based on where they sit in the scale from simplicity to complexity in their project’s geology. Perhaps with this as a guide we can reduce the number of projects where there is less than 50% accuracy in the geological predictions – such as the three highlighted by Lok.
- Regards,
Dr Trevor Carter P.Eng., C.Eng., C.Geol.
- Carter TG (1992) Prediction and uncertainties in geological engineering and rock mass characterization assessment. In: Proceedings of the 4th Italian rock mechanics conference, Torino, pp 1.1–1.22
- Carter, T. G., & Marinos, V. (2020). Putting geological focus back into rock engineering design. Rock Mechanics and Rock Engineering, 53(10), 4487–4508. doi:10.1007/s00603-020-02177-1
- Venturini, G., Bianchi, G.W., and Diederichs, M. (2019). How to quantify the reliability of a geological and geotechnical reference model in underground projects. 2019 RETC Rapid Excavation and Tunneling Conference
Q-system references in the TunnelTalk Archive– TunnelTalk May 2012
Geotechnical concerns for deep mountain drives – TunnelTalk May 2012
In search of the ideal TBM specification– TunnelTalk June 2018
Delay to Crossrail completion is outrageous
-
Article referenceMore money and time needed to rescue completion of Crossrail in London - TunnelTalk December 2018
- Feedback from: Richard Lewis, Hong Kong
- I recently came across a TunnelTalk article from June 2015 celebrating the completion of all tunnelling and TBM work on Crossrail. This was after the first drive started in May 2012. That was just about 42km of tunnel and around 13 stations excavated in three years. Arguably the most difficult and arduous task of the project.
- It is now five years later and still it is not complete, and now I read in TunnelTalk that further increases in costs and time are required before the project can be completed. Full opening by mid-2022 has now been put in doubt. That is seven years after excavation is complete!! It is absolutely unbelievable.
- How can it be that no proper and full explanation is made public and that no-one is held responsible for this abominable and appalling performance of the post-excavation activities of the project. It is likely that the stigma of this terrible performance will also rest on the shoulders of the tunnelling Industry and that is beyond being unfair. It is criminal. It deserves a full enquiry which should exonerate the tunnel/construction industry and put the blame where it should be – wherever that is.
- Best regards,
Richard Lewis
YL Associates Limited
Hong Kong -
Article referenceEditor's Desk comment – TunnelTalk Alert 13 December 2018
- Feedback from: James Wonneberg
- In response to the TunnelTalk Editor’s Desk question about why underground projects tend to slip during the finishing phases, I would submit that tunnel boring machines and ground conditions have rightfully earned their place in most risk assessments today, but as an industry we do not always give enough weight to the ‘hard things’ that project teams must still overcome after excavation is out of the way.
- These include complex design and construction coordination between civil work and systems installations, handovers from one contract to another, commissioning, and readiness to operate the completed facility.
- Sometimes working backwards can help shine a light on these challenges. For example, start with the desired opening date for the new facility, then work backwards from there, noting all the detailed steps in reverse, including the owner’s acceptance process, testing of each system, construction staging area handovers, etc.
- When you complete this exercise, using realistic durations, you may find that work should have started six months ago and you are already late!
- Seven-time World Champion chess player Jose Raul Capablanca said it best:
- In order to improve your game, you must study the end game before everything else. For, whereas the endings can be studied and mastered by themselves, the middle game and opening must be studied in relation to the end game.
- Kind regards,
James Wonneberg, PE, CCM
Resident Engineer at McMillen Jacobs Associates
Co-Founder of GraphicSchedule
More money rescues completion of Crossrail – TunnelTalk December 2018
Industry and Company News Briefs– TunnelTalk 20 July 2020
Landmark breakthrough for UK Crossrail– TunnelTalk June 2015
Crossrail launches first TBM – TunnelTalk May 2012
Why is it that the final phases of underground projects blow the budget and the schedule?
Covid impact on 2021 business travel plans
05 Nov 2020
-
Article referenceOptimism for events into 2021 and beyond – TunnelTalk October 2020
- Feedback from readers
- Cautious optimism for being able to attend physical conferences and events into 2021, as reported last week, attracted Feedback from readers about the prospects of being able to travel to international fixtures given renewed lockdown directives in several European countries and the inexorable rise in the number of Covid pandemic cases in northern hemisphere countries as they go into the winter season.
-
Google tracking of the pandemic spread as of 5 Nov 2020
- This prompted a review of the Covid situation globally and an internet search found several Covid tracking services that provide information about the current situation worldwide and nationally (Fig 1). National governments have information pages about regulations for travellers entering their countries and for their citizens travelling to other countries. The advice ahead of booking any international travel is to check these directives, with many countries demanding proof of a negative Covid test within hours of boarding a plane to make a trip and others limiting departure and entry of flights to and from different countries.
- While there is a yearning to be able to resume international business travel, the overarching mood is that there remains a lack of personal confidence to make travel arrangements, even if that is possible in reality. Staying at home and limiting association in large gatherings remains the general advice from scientists and politicians in Europe and elsewhere in the hardest hit countries.
Finding a solution for who should choose the TBM
-
Article referenceWho should choose the TBM?
- Feedback from: Dean Brox, Canada
- The points are a smoke screen to the real problem, which is poor quality GBRs. The liability only gets confused when the project designers/Clients produce a poor GBR which is overly optimistic on the ground conditions, and then, when things go sideways, they want to blame it all on the Contractor and the TBM supplier.
- Regards,
Dean Brox,
Independent Consultant,
Canada - Feedback from: Colin Warren, UK
- Agreed that a more open collaborative approach to TBM selection as elated to the expected ground conditions is required and do not believe the GBR entirely fulfils that role. If allowance was given to this including more open discussion and agreement many disputes regarding expected to encountered ground conditions in relation to TBM selection would be avoided.
- Regards
Colin Warren
UK
A duty to learn from failures
-
Article referenceEditor’s Desk comment of 23 July 2020
- Feedback from: Donald Lamont, UK
- Dear Editor,
- I started my site career on projects under the 5th and 6th Edition of the Institution of Civil Engineers form of contract. Normal practice was that the design consultant, normally a professional practice partnership with unlimited liability, became The Engineer under the contract and oversaw construction. Design preceded construction. This all had the advantage of continuity of knowledge between design and construction phases. In place of self-certification QA systems, the Resident Engineer’s staff had the knowledge, authority and independence to make sure the work was done correctly. I never once, in ten years on site, filled in a non-conformance report, but I did tell the contractor on many occasions that a load of concrete or other material should not be used in the works. Mistakes did occur but, with good will on both sides, could be resolved in accordance with the conditions of contract.
- Now, design consultants are large limited companies, often run by managers with limited engineering knowledge and many designers lack practical site experience.
- Any incident involving actual or potential ill health or injury will be investigated independently by the regulatory authorities.
- A Dispute Resolution Board can be a great help, but should we not be seeking to reduce the potential for disputes in the first place, such as by improving practical engineering competence and learning from the mistakes of others, as suggested by James Thomson?
- Dr Donald Lamont C.Eng FICE
Hyperbaric and Tunnel Safety Ltd - Feedback from: Dean Brox, Canada
- There is certainly a duty to learn from past failures, regardless of how embarrassing it may be for the designers, reviewers and other parties involved, but of course this is not extinctive for humans.
- Forensic investigations should be institutionalized as a part of engineering planning, design and execution and be completed by an independent party without prior involvement and allowed to be completed without any due influence from Clients who do not want their project to acquire a negative label from a failure. Designers and Clients should also not adopt the excuse that insurers will pay for all failures as a reason to not learn from the past.
- There appears to be ample evidence of ongoing errors and repeated poor practice in the tunneling industry, such as with the design of partially lined hydroelectric tunnels in non-durable geological conditions that have led to very serious failures and significant losses – six in the last decade – all of which were design related errors and not related to construction quality defects. One of the key reasons for these ongoing engineering errors is the complete lack of review and appreciation of historical design and construction practices and recognizing the lessons to be learned from the past problems and failures. It appears that the practice today has become ‘there is nothing to learn from the past’ and that everything can be found and learned from Google.
- This industry, and likely many others, are unfortunately producing Google engineers, where some young professionals believe they are in fact ‘experts’ or senior managers with only less than 10-15 years of experience and fully capable of making high risk decisions without senior or independent review. Many of us are certainly guilty of a lack of mentoring of young professionals in today’s fast-paced industry where there is a shortage of senior professionals with adequate experience for mentoring and this has also contributed to the poor practices and errors that have occurred.
- Another serious error in the industry is the assumed automatic exporting of design practices from one country to others where the site conditions and risk tolerance may not be suitable for such practices.
- Finally, Clients and Designers should recognize that risk management practices and workshops do not provide a guarantee against errors especially when most do not engage independent ‘eyes’ but rather depend only on the eyes of the project team who will not admit to any shortcomings or lack of recognition of risk scenarios from past experience.
- Sincerely,
Dean Brox,
Independent Consultant
Vancouver, Canada - Feedback from: James Thomson C Eng
- We learn more from our mistakes than we do from our successes. However, today, most failures are never properly reported due to legal liability considerations.
- James Thomson C Eng
- Feedback from: Wolfgang Bönsch, Gerrmany, in response to Prasad Sen, India
- Dear Siba,
- I appreciate your reply. I think the system for DRBs could be used for forensic research and be part of contracts. The DRBF also started small with the idea to support all parties and help to avoid problems. They are now part of FIDIC contracts.
- Institutionalising the forensic investigation has to be sold as a commercial advantage for the future to learn from failures no matter whose responsibility it might be, and employing a university or research facility, on the basis of Employer and Contractor, equally sharing the cost and receiving the outcome for improved quality control and better risk management and estimation. The university can use the data for further research and development, interfacing management of the many disciplines in tunnelling.
- I have been working on research and development for the company Wayss & Freytag, now part of the BAM Group, that held the patents for the slurry, hydroshield and Mixshield TBMs before they sold the Mixshield to Herrenknecht. Our R&D department was closed, because it was considered R&D can be bought from universities if needed. Bad management decisions happen all the time.
- That took me back to working on site where I have had an interesting career as a “Tunnel Tramp” as a good friend put it.
- Regards,
Wolfgang Bönsch, Germany - Feedback from: Siba Prasad Sen, India, in response to Bönsch, Germany
- Dear Wolfgang,
- Thank you for supporting the idea of institutionalising the forensic investigation of failures. DRBs or Dispute Resolution Boards are helping in many cases to resolve the dispute on risk sharing, but my purpose of writing was primarily to document the reason and stage of failure in a scientific way. Such documents will be a treasure of knowledge for future understanding and, obviously, can help in dispute resolution.
- It is, however, difficult to sell the idea specially on commercial rules based contracts, as they are ambiguous. The contract will be best, probably, if it can be made after execution!
- Regards,
Siba Prasad Sen, India - Feedback from: Wolfgang Bönsch, Germany
- Dear TunnelTalk,
- I write in support of the suggestion by Siba Prasad Sen (see below) to institutionalize forensic investigation as a part of engineering planning, design and execution. I think this is a brilliant idea.
- Often one of the problems is that the same Design Consultant is often hired as Supervision or Project Management Consultants for the same project. This gives the opportunity (which is quite human) to shift design flaws and errors to the Contractor or Client which doesn’t help the common goal, which is the success of the Project. Disputes are inevitable!
- A Dispute Review or Resolution Board from the beginning of the Project is a great help to all parties involved. Visit the Dispute Resolution Board Foundation for additional information.
- Best regards,
Wolfgang Bönsch, Germany - Feedback from: Siba Prasad Sen, Independent Consultant
- Dear Editor,
- You raise a valid question or issue - to learn from previous mistakes.
- I think the general human tendency is to not look back to failure with a critical mind. Instead, people become busy immediately to rectify or take corrective measures, even if that may be patchy. In reality it takes time for a person or persons who are involved in the planning, design and execution of works that have failed to understand what actually went wrong. But before that, an all-encompassing alternative solution is found and executed, and the issue is forgotten and transferred to legal and contractual experts.
- If it was due to a design fault, and the designer goes on ruminating in his mind maybe for a reasonable time or so, he can then realise the mistake which may not be, or may be, due to design fault, and may be due partly to planning fault, and/or partly execution fault. Even if the reason of the failure is easily, or difficultly, understood by a systematic forensic examination, people do not want to discuss this openly due to the contractual complexity between different parties, and its legal and financial implication.
- Hence the knowledge generated by a failure sometimes gets covered by mist and storm of arguments. But these studies generate knowledge and wisdom, not only for any particular person, but for all engineers. Whether due to fault in planning or design or implementation, all of us learn from it.
- Sometimes I wonder if forensic investigation should be institutionalised as a part of engineering planning, design and execution.
- Thank you,
Regards,
Siba Prasad Sen, Independent Consultant - Search <failures> to find other Feedback items that discuss the topic of failures and learning from the experiences
Hydropower watercourse failures - risks and causes– TunnelTalk March 2020
North America DRBs-knowing and playing by the rules– TunnelTalk August 2008
Road to litigation and possible bypasses– TunnelTalk January 2020
Nuclear Waste Focus: Underground nuclear power plants? Yes – why not?
-
Article referenceGlobal dilemma of nuclear waste management – TunnelTalk June 2020
- Feedback from: Nick Barton, Independent Consultant
- Dear TunnelTalk,
- The article presents the suggestion of building nuclear power plants and their reactors underground. Selecting the geological locations would be difficult, significantly less than the geological study and investigation for siting a nuclear waste repository, but technically it is possible. The underground location of reactors would have huge safety bonuses and we know that caverns of 50m span in moderate to good rock are of limited problem.
- For operation of nuclear power plants underground, an artificial lake with sufficient area for cooling lagoons, and entry into rocky hillsides to no more than 100m-200m vertical depth are not insurmountable siting targets. Q-values of the host rock would need to be reasonable.
- At the Gjøvik underground sports hall cavern at Lillehammer in Norway, with its span 62m, the range of Q for the host rock was 2 to 32 with a mean of about 10. The mean RQD was only 60 and the rock UCS was 90 MPa.
- As a further example of what is possible underground, we can refer to the Baihetan hydropower project in China where they have such huge machine halls beneath either side of the fast flowing Jinsha River to generate electricity via 16 x 1,000 MW capacity turbines. The machine halls measure an outstanding 453m long x 35m span x 89m high. There are 130km of associated access, river diversion and pressure tunnels. The caverns are currently the largest in the world.
- Sincerely,
Nick Barton
Independent Consultant
Iconic underground structures– TunnelTalk September 2010
Nuclear Waste Focus: Insurance concerns about nuclear waste management
-
Article referenceGlobal dilemma of nuclear waste management – TunnelTalk June 2020
Editor’s Desk comment – TunnelTalk Alert 04 June 2020
- Feedback from: Markus Klein
- Dear TunnelTalk,
- I certainly cannot claim to be an expert in this subject matter, but the following, not necessarily technical, points might capture interest.
-
- I believe we can agree that disposing of nuclear waste, in particular severely contaminated nuclear waste, comes with a price tag.
- The questions are, who is responsible for the disposal and who pays?
- Liabilities for the safe and secure disposal of nuclear waste are sitting not only with parties involved in operation of nuclear (fission) power plants and spent nuclear fuel recycling plants but also, to a certain degree, with the insurance/reinsurance industry and the states, representing nuclear re/insurance pools. It is complicated.
- The question here is, these stockpiles of nuclear waste are not popping out of the blue, right? Has the whole supply and responsibility chain been thought through thoroughly in the first place?
- Technically, I assume you advocate in the TunnelTalk Editor’s Desk comment, an underground, nicely engineered, safe and secure tunnelled deposit solution, but for how many years?
- Tunnel industry professionals know much better and in far more granular detail than I, what an interpretative geotechnical report entails, and exactly as the name says, there is interpretation of certain facts and figures and there is likely to be more than one interpretation on hand. I recall a court decision where a nuclear power plant operation was denied because documents, presented retrospectively, from a monastery dating back hundreds of years, note the monitoring of earthquakes in the region. A peril that could affect the underground deposit solution as well, do you think?
- Another layer of complexity comes with
- some sort of time pressure as this contaminated waste is piled up already,
- the political scene in any country and the challenge of selling the proposal to the people, and
- globally, the rather less than unified political scene already struggling to come to grips with some pretty fundamental issues, including trade agreements as an example.
- In conclusion, whilst I like your thought and approach, technically, economically and from a feasibility point of view, at this stage I would not bet on an international treaty, agreed and signed, to tackle nuclear waste underground deposit solutions in the near future, say the next 10-20 years, unless political pressure piles up to deliver on reducing greenhouse gases in the absence of nuclear fusion technology, and the renaissance of nuclear fission.
- Regards,
Markus Klein
Berkshire Hathaway Specialty Insurance,
Sydney NSW 2000, Australia
Water inflow issues in deep tunnels beneath high overburdens
-
Article referenceLötschberg plans for long-term water inflow repair – TunnelTalk May 2020
- Feedback from: Dean Brox
- Nice follow up on the Lötschberg water inflow incidences.
- I note however, that the maximum overburden in the karst zone is actually 900m since it goes all the way to the top of the rock unit to where it is exposed on the surface (Fig 1), and a few comments to add.
-
- A tunnel lining with a membrane cannot withstand 90 bars external pressure.
- Open boreholes into the tunnel allows groundwater to flow and transport fines into the tunnel and subject to the full pressure, possibly contributing to dissolution, and the large lateral extent of the rock unit providing unlimited storage.
- High pressure grouting and enhancement of the lining required to prevent further rupture of the membrane a 90 bar vault will be needed requiring an extensive excavation with removal of the existing lining and the casting of a thick reinforced new lining.
- The current drainage solution will require ongoing maintenance.
- This is going to be a bigger job than expected and take longer than anticipated.
- Best regards,
Dean Brox,
Independent Consultant
-
Article referenceLötschberg water inflow explained – TunnelTalk May 2020
Editor’s Desk comment of 07 May 2020 - Feedback from: Trevor Carter
- Great Lötschberg articles and I totally agree. Issues that arise in operating tunnels should be treated seriously. Mud migration in karst systems can lead to very major inflows, and possibly damage to the lining. At 400m+ cover, water pressure on the back of the lining will be significant, but mud impact dynamic pressures can be many times greater, as commonly considered in the design criteria for deep mining bulkhead plugs. With two significant mud impact events in the Lötschberg, the lining may have already been cracked. Needs checking out.
- Sincerely,
Dr Trevor G. Carter
Golder Associates
Toronto, Canada
Geotechnical concerns for deep mountain drives – TunnelTalk May 2012
- Dear TunnelTalk,
- We read at intervals in excellent journals, or in published papers or at a lecture about what can go seriously wrong in our challenging underground environment.
- Instead of reading or hearing of a hydropower head-loss, or mine accident, or a near-miss during excavation, it is almost refreshing - though no less serious - to view the muddied train that exited the Lötschberg recently and as seen in the informative TunnelTalk report. A challenging problem, caused perhaps by an unknown thickness of immediately surrounding rock in karstic terrain, despite 400m depth, or somehow a serious increase in water pressure (quite feasible in karst caverns) or deformation-caused cracking, and then leakage, the list of possibilities emphasises the hydrogeological risks, especially in the case of karst.
- But there are also risks with choice of method. The leakage of water, and mud, serves to warn us of the questionable long-life performance of an easily clogged drainage fleece. There are also the many kilometres of welds in the membrane and the radial joints in successive concrete pours. These are actually absent when using sufficiently thick longitudinally sprayed shotcrete. There are no radial joints, and steel fibre shotcrete has extremely low permeability, in the panel-sprayed range of 10E-10 to 10E-12m/s.
- So, what are the best choices? Frankly it is not felt that the style of belts-and-braces incorporated in double-shell systems is the right answer. Another choice is one that automatically includes probe drilling through the crucial rock surround with rock mass improvement, which has clear advantages in karstic terrain. Systematic high-pressure pre-injection, with pressure suited to the rock and rock mass, remains a cost-effective solution.
- There are literally millions of kilometres of drill-holes used for construction of large dams where grout curtains are permanent and designed for a 100-year+ life. Pre-grouting umbrellas ahead of the face for high-speed rail tunnels of more than 100m2 in cross section, take 24-30 hours/cycle and provide for a guaranteed almost 20 hours/week of full-face excavation. Pre-excavation grouting is known, and has been 3D-measured, to cause rotation of the 3D permeability tensors, and their magnitude reduction, and modulus and velocity increase. In fact, the six Q-parameters may be effectively improved. The risk during construction is reduced dramatically by drilling 1-1.5km of holes every 15-20m of tunnel advance. Any damp spots in the shotcrete signal where a local post-injection hole is needed. This is not the case with the double-shell solution.
- Best regards,
Nick Barton
Independent Consultant
Norway
Sealing and drainage experiences in Swiss tunnels – TunnelTalk December 2018
Testing durability of PVC membranes– TunnelTalk October 2018
Environmental and lifecycle advantages of underground infrastructure
-
Article referenceEditor’s Desk comment of 16 Apr 2020
- Feedback from: James Hughes
- To the Editor,
- Transportation designers for years have ignored the use of tunnels in lieu of elevated structures that raise noise levels, separate neighborhoods and lower property values. Underground is by far the better solution for all modes of transportation to provide better neighborhoods for the citizens of the communities these projects serve.
- Regards,
James H J Hughes III, PE
President
JH3 Heavy Civil Equipment LLC
Underground Construction Gear
Underground developments on Seattle LRT– TunnelTalk April 2020
Toronto invites qualification for new metro projects – TunnelTalk April 2020
Sydney plans a major metro expansion – TunnelTalk February 2020
WestConnex secures Aust$1.7 billion in funding – TunnelTalk December 2016
Underground excavation wish list – TunnelTalk January 2020
Support and scepticism for advance of autonomous TBMs
-
Article referenceAward-winning autonomous TBM operations – TunnelTalk December 2019
- Feedback from: Tony Pattison
- I was involved with ZED on the installation of the autosteer system on the Wirth TBM in Clarens on the Lesotho Highlands Water Project back in 1991. It seems a long time ago and I am amazed that all TBMs are not now fully automated, given the advances we achieved all those years ago.
- I work on satellites these days so am not up to date with what is happening in the tunnelling business lately, but I would have thought adding steering control to a modern machine would be an almost trivial task and it should be on every machine. I would also expect any reasonable sized project these days would insist on a TBM guidance system and with a lot of machine monitoring and instrumentation, so connecting the two together, to improve smoothness and consistency of alignment, would be a really effective benefit for very little cost or effort really.
- Sincerely,
Tony Pattison CEng, BSc, MIET
Senior Electronic Engineer
Surrey Satellite Technology Ltd, UK
- Feedback from: A TunnelTalk reader
- Yes, the push to TBM automation is incredibly interesting. However, I am absolutely concerned by that discussion. It will move responsibility from the operator to the manufacturer, much like self-driving cars, and while the mechanical engineer in me is jubilant, I do not yet know how the legal frameworks we have will react.
- Sincerely,
A TunnelTalk reader
Award-winning autonomous TBM operations– TunnelTalk December 2019
Equipping TBMs for tough conditions – TunnelTalk November 2019
Achievements celebrated in 2019 ITA Awards– TunnelTalk November 2019
Hydropower waterway designs and recommendations
-
Article referenceHydropower watercourse failures - risks and causes – TunnelTalk March 2020
- Feedback from: Fabrizio Bove, Project Manager, Seli Overseas
- Thank you for the interesting analysis carried out and good suggestions shared.
- Since I had the challenging opportunity to work for the rehabilitation of the Estì headrace tunnel in Panama, I would like to add and share some issues for further considerations:
- To: Failures due to the incomplete identification of weak or critical geological zones
In the case of Estì, the failure occurred mainly because horizontally bedded weak layers that ran parallel to the tunnel axis in several areas and were not visible during excavation. In other words, during the face inspections the rock mass had been recorded as self-stable and sound with high value rock mass indexes, thus leading to a choice for a softer lining of shotcrete. As a result, only a complete overview, focusing of the stabilization of the on-going advance core and fully appreciating the in-situ 3D geology and the nature and pace of future hydraulic loading for the tunnel, could improve the choice of the permanent lining and stability. - To: A general industrialized approach to excavation for example, using TBMs with standard reinforced precast segments or conventional methods with cast-in-situ
The suggestion is that these should have led to better results, avoiding the uncertainty of shotcrete for long-term stability. Most of the time the application of quality shotcrete relies on operators and fibres randomly distributed. More difficult quality control measures are also required especially for larger diameter tunnels. - To: An “ad hoc” approach and particular care may improve the results in case of critical areas
Where the biggest collapse of about 14,000m3 occurred in Estì, at least three factors could have hampered the situation: - A steep geometrical change of the tunnel alignment,
- Low overburden and
- Parallel alignment of the soft/weak strata with the tunnel axis.
- To: Choice of contract type
An EPC contract was used for the main project procurement and also for the Estì rehabilitation phase in 2011 and 2012 and with good achievements. Obviously however, a stronger control by the Engineer is needed in these cases. - To: A contractual “risk-sharing approach” between Employer and Contractor
In the case of unforeseen and unforeseeable events this can be the best option, both in terms of cost control and timely reaction and application of solutions. - Best regards,
Fabrizio Bove
Project Manager
Seli Overseas
- Feedback from: Chris Breeds
- Great article Dean. Very informative and great examples.
- Best regards,
Chris Breeds
- Feedback from: Nick Barton, Independent Consultant
- Dear TunnelTalk,
- It is always interesting to read of tunnel failures, from which we all learn. I have two points in response.
- In his interesting and well-illustrated review, Brox has suggested using “other than rock mass classification methods” for application of final support and linings. There is nothing wrong with this suggestion except that it ignores the contribution of such methods to thousands of kilometres of hydropower tunnels and considerable cost savings for owners. If mistakes are made in application of the methods due to oversight, especially in the case of faulted rock, then lessons need to be learned by those involved. Incidentally the Ituango case, the failure erosion cone is much larger than described and is a special case of optimism in diverting water with a peak velocity of up to 10m/sec around a remarkably tight bend, both of which are entirely different to the typical 1.5-2.5 m/sec velocities in the case of hydropower tunnels. Design for velocities of 1.5-2.5 m/sec have been and are the basis of Q-system case records. With Eda Quadros, I have prepared a paper for Eurock 2020 titled Some lessons from single-shell Q-supported headrace and pressure tunnels that may not now be presented due to Covid-19 postponements but may become available in published proceedings of Eurock 2020 planned for 15-19 June 2020 in Trondheim, Norway.
- Secondly, Brox recommends independent checking of waterway tunnel designs. I agree that this could, in principle, be valuable. I have reservations however based on what is available outside of the use of more careful rock mass characterization and use of empirical methods, like the Q-system which probably has the most relevant database. It should not be forgotten that there are thousands of kilometres of such waterways, and many hundreds (actually thousands) of economic projects as a result of the single-shell type of support, which, as pointed out by many, needs to consider the intended use of the tunnel. As indicated above, if a water velocity, as in the case of a river diversion, is chosen by a designer that is well outside the database (for example 10m/sec as compared with a conventional 2m/sec velocity), then one is asking for potential trouble, if the tunnel support, also of the invert, is not dimensioned accordingly.
- Having reviewed many projects over the years, and having experience of a specific international court case, it is evident that numerical modelling is frequently too much relied upon. These experiences have also demonstrated the severe limitations of popular numerical modelling methods, those that produce the colourful appendices (and maybe pay-raises), might well be used by engineers engaged to carry out independent checking with the assumption that they are more reliable and sophisticated than rock mass classification and empirical methods. The exaggerated so-called plastic zones of supposedly jointed models, or of the simpler continuum models, has led to jokes about needing snow shoes so as not to sink in the models as they show quite different behaviour to more reliable models with longer track records.
- Of course, it is also possible to misuse the more reliable codes and their longer track records by, for example, modelling with exaggerated joint continuity. There are hundreds of examples of this. In fact, it is found that a super-simple empirical model, linking deformation, tunnel span and the Q-value, provides a far more accurate check of potential deformation, as monitored subsequently at the completed project, than the exaggerated models. With more realistic engineering- geologist-generated joint continuity and its digitization, a more realistic and smaller deformation is predicted which agrees well with the simple empirical check.
- Best regards,
Nick Barton
Independent consultant
Norway
Panama awards urgent Esti headrace repair– TunnelTalk December 2011
Panama adopts EPC contracting for Esti scheme– TunnelTalk June 2003
Single-shell lining design and advantages – TunnelTalk February 2020
Q-system references in the TunnelTalk Archive
Support and scepticism for advance of autonomous TBMs
-
Article referenceAward-winning autonomous TBM operations – TunnelTalk December 2019
- Feedback from: Tony Pattison
- I was involved with ZED on the installation of the autosteer system on the Wirth TBM in Clarens on the Lesotho Highlands Water Project back in 1991. It seems a long time ago and I am amazed that all TBMs are not now fully automated, given the advances we achieved all those years ago.
- I work on satellites these days so am not up to date with what is happening in the tunnelling business lately, but I would have thought adding steering control to a modern machine would be an almost trivial task and it should be on every machine. I would also expect any reasonable sized project these days would insist on a TBM guidance system and with a lot of machine monitoring and instrumentation, so connecting the two together, to improve smoothness and consistency of alignment, would be a really effective benefit for very little cost or effort really.
- Sincerely,
Tony Pattison CEng, BSc, MIET
Senior Electronic Engineer
Surrey Satellite Technology Ltd, UK
- Feedback from: A TunnelTalk reader
- Yes, the push to TBM automation is incredibly interesting. However, I am absolutely concerned by that discussion. It will move responsibility from the operator to the manufacturer, much like self-driving cars, and while the mechanical engineer in me is jubilant, I do not yet know how the legal frameworks we have will react.
- Sincerely,
A TunnelTalk reader
Award-winning autonomous TBM operations– TunnelTalk December 2019
Equipping TBMs for tough conditions – TunnelTalk November 2019
Achievements celebrated in 2019 ITA Awards– TunnelTalk November 2019
Hydropower waterway designs and recommendations
-
Article referenceHydropower watercourse failures - risks and causes – TunnelTalk March 2020
- Feedback from: Fabrizio Bove, Project Manager, Seli Overseas
- Thank you for the interesting analysis carried out and good suggestions shared.
- Since I had the challenging opportunity to work for the rehabilitation of the Estì headrace tunnel in Panama, I would like to add and share some issues for further considerations:
- To: Failures due to the incomplete identification of weak or critical geological zones
In the case of Estì, the failure occurred mainly because horizontally bedded weak layers that ran parallel to the tunnel axis in several areas and were not visible during excavation. In other words, during the face inspections the rock mass had been recorded as self-stable and sound with high value rock mass indexes, thus leading to a choice for a softer lining of shotcrete. As a result, only a complete overview, focusing of the stabilization of the on-going advance core and fully appreciating the in-situ 3D geology and the nature and pace of future hydraulic loading for the tunnel, could improve the choice of the permanent lining and stability. - To: A general industrialized approach to excavation for example, using TBMs with standard reinforced precast segments or conventional methods with cast-in-situ
The suggestion is that these should have led to better results, avoiding the uncertainty of shotcrete for long-term stability. Most of the time the application of quality shotcrete relies on operators and fibres randomly distributed. More difficult quality control measures are also required especially for larger diameter tunnels. - To: An “ad hoc” approach and particular care may improve the results in case of critical areas
Where the biggest collapse of about 14,000m3 occurred in Estì, at least three factors could have hampered the situation: - A steep geometrical change of the tunnel alignment,
- Low overburden and
- Parallel alignment of the soft/weak strata with the tunnel axis.
- To: Choice of contract type
An EPC contract was used for the main project procurement and also for the Estì rehabilitation phase in 2011 and 2012 and with good achievements. Obviously however, a stronger control by the Engineer is needed in these cases. - To: A contractual “risk-sharing approach” between Employer and Contractor
In the case of unforeseen and unforeseeable events this can be the best option, both in terms of cost control and timely reaction and application of solutions. - Best regards,
Fabrizio Bove
Project Manager
Seli Overseas
- Feedback from: Chris Breeds
- Great article Dean. Very informative and great examples.
- Best regards,
Chris Breeds
- Feedback from: Nick Barton, Independent Consultant
- Dear TunnelTalk,
- It is always interesting to read of tunnel failures, from which we all learn. I have two points in response.
- In his interesting and well-illustrated review, Brox has suggested using “other than rock mass classification methods” for application of final support and linings. There is nothing wrong with this suggestion except that it ignores the contribution of such methods to thousands of kilometres of hydropower tunnels and considerable cost savings for owners. If mistakes are made in application of the methods due to oversight, especially in the case of faulted rock, then lessons need to be learned by those involved. Incidentally the Ituango case, the failure erosion cone is much larger than described and is a special case of optimism in diverting water with a peak velocity of up to 10m/sec around a remarkably tight bend, both of which are entirely different to the typical 1.5-2.5 m/sec velocities in the case of hydropower tunnels. Design for velocities of 1.5-2.5 m/sec have been and are the basis of Q-system case records. With Eda Quadros, I have prepared a paper for Eurock 2020 titled Some lessons from single-shell Q-supported headrace and pressure tunnels that may not now be presented due to Covid-19 postponements but may become available in published proceedings of Eurock 2020 planned for 15-19 June 2020 in Trondheim, Norway.
- Secondly, Brox recommends independent checking of waterway tunnel designs. I agree that this could, in principle, be valuable. I have reservations however based on what is available outside of the use of more careful rock mass characterization and use of empirical methods, like the Q-system which probably has the most relevant database. It should not be forgotten that there are thousands of kilometres of such waterways, and many hundreds (actually thousands) of economic projects as a result of the single-shell type of support, which, as pointed out by many, needs to consider the intended use of the tunnel. As indicated above, if a water velocity, as in the case of a river diversion, is chosen by a designer that is well outside the database (for example 10m/sec as compared with a conventional 2m/sec velocity), then one is asking for potential trouble, if the tunnel support, also of the invert, is not dimensioned accordingly.
- Having reviewed many projects over the years, and having experience of a specific international court case, it is evident that numerical modelling is frequently too much relied upon. These experiences have also demonstrated the severe limitations of popular numerical modelling methods, those that produce the colourful appendices (and maybe pay-raises), might well be used by engineers engaged to carry out independent checking with the assumption that they are more reliable and sophisticated than rock mass classification and empirical methods. The exaggerated so-called plastic zones of supposedly jointed models, or of the simpler continuum models, has led to jokes about needing snow shoes so as not to sink in the models as they show quite different behaviour to more reliable models with longer track records.
- Of course, it is also possible to misuse the more reliable codes and their longer track records by, for example, modelling with exaggerated joint continuity. There are hundreds of examples of this. In fact, it is found that a super-simple empirical model, linking deformation, tunnel span and the Q-value, provides a far more accurate check of potential deformation, as monitored subsequently at the completed project, than the exaggerated models. With more realistic engineering- geologist-generated joint continuity and its digitization, a more realistic and smaller deformation is predicted which agrees well with the simple empirical check.
- Best regards,
Nick Barton
Independent consultant
Norway
Panama awards urgent Esti headrace repair– TunnelTalk December 2011
Panama adopts EPC contracting for Esti scheme– TunnelTalk June 2003
Single-shell lining design and advantages – TunnelTalk February 2020
Q-system references in the TunnelTalk Archive
Hydro challenges in the Himalayas
-
Article referenceHydro TBM risk assessment and selection – TunnelTalk December 2020
- Feedback reply from: Siba Prasad Sen
- Dear Dean Brox,
- Thank you and in your reply you talk about the Bheri Babai project in Nepal. Since 2012 my involvement with that project was in preparing the feasibility of the project and subsequently till preparation of tender document for the tunnel including the bill of quantities and technical specification of the proposed contract for the Irrigation Department of the Government of Nepal. A reasonable study for feasibility was done and subsequently a good GBR (geotechnical baseline report) could be prepared because the tunnel alignment was accessible to a great extent, and Nepalese geologists with whom I worked for this project did a commendable job.
- What makes the situation worse in the Himalaya is the presence of high-pressure geohydrology which is not case in the Bheri Babai project. Hence risk was not that high. With long experience of the Himalayas during my engineering career with NHPC, the absence of high ground water tables and the absence of artesian wells along the tunnel alignment is a good sign for less trouble from water. But it is rare. However, the Bheri Babai TBM was well conceived and designed with all kinds of ground engineering provisions and it appears that there were competent engineers and operators, with thinking minds, who operated the TBM successfully.
- For Parbati II, where the TBM is still struck, the owner NHPC was able to construct successfully the two inclined pressure shafts, each of about 1.1km long and inclined on about 30 degrees, using an inclined TBM. Extending my previous logic here, the cover was not very high and followed the natural slope, and also, due to the same reason, the groundwater pressure was not high.
- NHPC was also successful on the Kishanganga hydro project in the western Himalaya State of Jammu and Kashmir, India, to excavate about 10km of the headrace by TBM in about 24 months. Here cover was very high, at up to 1,400m, but ground water was not the troubling force. The contractor was also competent.
- But all these are exceptions and not the trend. There are some TBM tunnels for different hydro projects which are unfinished, causing huge loss to the owner and also to the construction agencies. Until a reasonable method is found to undertake a satisfactory geological and hydrogeological investigation and plan for a sustainable excavation procedure for TBM applications, we are caught in Hobson’s choice with only one option on offer. Cost is also a big factor along with risk. There are many associated elements that require development.
- Sincerely,
Siba P Sen,
Former Director Technical NHPC Ltd, India
Presently Independent Consultant, New Delhi, India - Feedback from: Article author, Dean Brox
- Thank you Siba Prasad Sen for your Feedback (below) concerning hydro challenges in the Himalayas.
- The Himalayas are the most challenging and high risk regions for the construction of tunnels. However, the recent completion of the 12km headrace tunnel by a double shield TBM erecting a precast segmental lining for the Bheri Babai water delivery tunnel in Nepal within the lower area of the Himalayas is encouraging. This excavation approach has been proven on many projects through the past 20 years and was successful on the Bheri Babai alignment through medium strength sandstones under 800m of cover, without squeezing, and passing through a major regional geological fault without impact.
- Key lessons have been learned also in the Andes where shielded TBMs and precast segmental linings are finally successfully completing the long tunnels of the Alto Maipo project with good progress. These are now representing a low-risk design and construction approach for future safe excavation and system operations of hydro tunnels in high mountainous geologies.
- Thorough geological investigations and careful interpretations are needed on a case by case basis for planning future use of TBMs in the Himalayas.
- Best regards,
Dean Brox
Independent Consultant - Feedback from: Siba Prasad Sen
- India has been pursuing hydropower development for the past seven-or-so decades and today has about 45,000 MW of large and medium capacity installed. Some 90% of the capacity is in the Himalayas. Here, the high mountain peaks, monsoon-driven hydrology, seismic vulnerability, steep slopes and many geological faults are a real challenge for planning, designing and constructing long tunnels for hydro projects. To add to the woes, there are high ground water tables with large aquifers, innumerable shear zones, squeezing rocks, and very hard rocks that cause rock bursting.
- For such terrains, to plan a hydro tunnel of more than 5km requires extensive geological investigations and detailed probing of the actual ground is very much required. Constraints in investigations beyond surface mapping by geologists, which itself is very difficult due to the hostile terrain, leads to poor understanding of the ground conditions. That is why planners and designers in India prefer to use drill+blast technology for tunnelling. That way, the long tunnels can be aligned in a zigzag manner along the side slope of the mountain valley.
- The 510 MW Teesta hydro project has a 17.5km headrace tunnel. This tunnel has been aligned along the mountain slope as close as possible to the road and there are three obtuse bends in the tunnel. This has helped to reduce the rock cover, which helps investigations and enables better geological mapping. Such a layout also reduces overburden and the hydro-static pressure of the ground water table and reduces the probability of squeezing and rock bursting. But the availability of such a road cannot be assured, particularly with concerns surrounding the environment and wildlife. Permission for such an intermediate approach is being regularly denied by the Environmental and Forest Authorities.
- In the Parbati Stage II project, the tunnel was designed partly by drill+blast with a zigzag alignment and partly by TBM for 9km of the total 32km length. The project is ready for commissioning in all respects except the TBM is struggling to complete the job. The TBM portion of the tunnel has very high cover and a high ground water head of 10 to 12 bar. There are many major and minor faults along the alignment along with high ground water inflows and very hard quartzite. There is very slow progress due to many contractual issues, including inappropriate choice of TBM, which is an open gripper machine and of insufficient capabilities. Risk sharing for such projects by the the Government owner is almost impossible. The present type of contract for the job cannot manage the risk and the fire brigade are being called upon. I was wondering whether in the near future it will be possible for a TBM to excavate a tunnel in zigzag alignment. The Himalayas are waiting for it.
- Best regards,
Siba Prasad Sen
Tunnel engineer
India
Nepal proving TBM applicability in Himalayas– TunnelTalk February 2019
TBM rescue for Tapovan and Parbati hydro challenges – TunnelTalk December 2016
Modern large diameter rock tunnels – TunnelTalk April 2010
New award follows Seli Kishanganga success – TunnelTalk May 2014
Nepal proving TBM applicability in Himalayas– TunnelTalk February 2019
In search of the ideal TBM specification – TunnelTalk June 2018
Alto Maipo Chile granted notice to proceed– TunnelTalk December 2013
Geotechnical concerns for deep mountain drives – TunnelTalk May 2012
Modern large diameter rock tunnels– TunnelTalk April 2010
TBM excavation conquers Peruvian Andes – TunnelTalk January 2012
Laos headrace finishes early despite challenges– TunnelTalk March 2017
TBM rescue for Tapovan hydro challenge – TunnelTalk December 2016
Double shield for challenging Indian hydro drive – TunnelTalk April 2016
TBMs through on long hydro drive in Ecuador – TunnelTalk April 2015
Sympathy for contractor following SR99 jury verdict
-
Article referenceAppeal logged after jury finds for SR99 client – TunnelTalk December 2019
- Feedback from: Dr Peter J Tarkoy
- Is it possible that the contractor losing the court case might be attributed to a poor presentation of their position?
- Feedback from: Nick Barton
- On the face of it (the above balanced explanation) this seems like a tough decision against the consortium STP. They have my sincere sympathy - they did not deserve this - nor did the Owner of course - but whose fault was it? Hardly that of the consortium.
- Feedback from a reader in the UK
- I like your reporting of the trial in TunnelTalk.
The logic behind the decision is astounding. Although DRB decisions are non-binding, they are nevertheless the combined opinions of three knowledgeable experts, who understand the contract. What is more, the DRB is appointed mutually by the Owner and the Contractor and either party needs to have good reason for not accepting a DRB decision. What is really amazing is that a jury of citizens off the street, with no technical or contractual experience, should contradict the unbiassed verdict of three experts. - Feedback from a reader in the UK
- I like your report on Seattle contract. Feel more than a bit sorry for the contractors on the findings particularly as the DRB found otherwise, and the contractors seems to have done a lot to save overall delays to the project by construction of the interior structures and road decks concurrent with operation of the TBM.
- Feedback from: Chris Pressdee
- I find it unbelievable that they discarded the steel casing and journals from the encounter with the well.
- From the Editor: Court records of an evidentiary hearing on spoliation of evidence indicate that instructions were given by STP management to STP staff to retain all evidence recovered following the encounter with the well casing on 4 December 2013, as well as granite boulders retrieved from the TBM screw conveyor and its plenum after stoppage of the TBM on 14 December. The pieces of well casing and boulders were stored on a wooden pallet in the job site yard. They were not moved, as intended, to a secure warehouse where spare parts and other materials and equipment for the project were housed. It was during February 2014 and after an instruction to “clean up” the job site area that the wooden pallet and its contents were noticed missing and described in court depositions as “disappeared”. Other pieces of the well casing from the plenum were retrieved and stored securely at the warehouse for further examination.
- There was no explanation offered to the court hearing for the missing journal. The journal documented the daily notes and events by the STP Deputy Project Manager for the period from December 2013 to February 2014, including notes of communications and instructions to other STP managers and staff. There were several of these journal notebooks and although described as personal journals, they were all handed over when requested by counsel. Of several journals, three journals covering different time periods were found missing. One was later found; the second was reported as stolen with a laptop computer as a result of a works vehicle break-in; and the third, for the period December 2013 to February 2014 remained lost.
- The court hearing into spoliation of evidence found that STP “did not intentionally destroy or hide” the pipe pieces or boulders or the journals but did find that the losses of the pipe pieces and boulders were “not innocent or accidental” and that the losses of all three pieces of evidence and the delay in admitting to the losses of the pipe pieces and boulders by STP to the client WSDOT, did constitute spoliation of evidence but did not provide grounds for dismissal of the court case and its trial.
STP wins latest round of Seattle DRB claims – TunnelTalk February 2015
DRB examines Bertha obstruction case – TunnelTalk May 2015
WSDOT “concern” over DRB obstruction ruling– TunnelTalk May 2015
Adding to the wish list and list of projects in progress for the new decade
-
Article referenceDiscussion Forum: Smooth sailing into the 2020s – TunnelTalk January 2020
- Feedback from: Tunnel enthusiast Shashikantha in Bangalore, South India
- Thank you for considering this for adding to the wish list.
-
Fig 1. Route of the proposed highway between Bangalore and Mangalore (inset)
- If you are familiar with the geography of South India, Bangalore is on an elevated plateau of 1,000m above sea level right in the middle of the two port cities of Chennai and Mangalore (Fig 1). There are no challenging mountain ranges between Bangalore and Chennai, but there is the formidable Western Ghats on the route west to Mangalore. To preserve the ecology of the Ghats, while not hampering the growth of Bangalore, which needs access to a sea port on the west coast, a road tunnel of 29km is being considered. It will be challenging work due to the elevation differences and the prevailing geology. It has been discussed for some time and perhaps this decade is the decade in which it will advance.
- Feedback from: Michael M
- Avid reader of TunnelTalk here.
- Just a small comment regarding the Discussion Forum: Smooth sailing into the 2020s. I thoroughly enjoyed reading this piece. There are however, a few projects in Europe that probably warranted a mention as they are among the largest, if not the largest, in Europe at present:
-
- The Grand Paris Express: 200km of new metro with 68 underground stations, requiring some +/-30 TBMs. Large portions already under construction with many more contracts to be awarded and started this year.
- The high speed rail line between Lyon, France and Turin, Italy (TELT). The four contracts for the base tunnel under the Alps are going out to RFP (requests for proposals) early this year. The twin tube base tunnel has a length of 57km.
- Keep up the great work!
- From the Editor: Thank you for the Feedback and for adding these important projects to our works in progress during 2020 and for your appreciation of the magazine. We have plans to add to our current Archive coverage of the two mega-projects during 2020 to bring the readers up to date.
Underground excavation wish list – TunnelTalk January 2020
Reintroduction to mega-TBM advantages in India – TunnelTalk January 2009
Paris advancing its mega metro expansion – TunnelTalk July 2017
Grand Paris Metro progresses with Line 16 awards – TunnelTalk October 2018
Shaft solution for Paris interchange station– TunnelTalk October 2019
Satellite ground monitoring for Paris Metro works – TunnelTalk May 2018
Progressing the Lyon-Turin base rail link – TunnelTalk August 2013
Consideration for potential causes of cracking segmental linings
-
Article referenceCracking of segmental lining under investigation – TunnelTalk September 2019
- Feedback from an engineer in Turkey who knows the project and has requested withholding of details for professional career reasons
-
No cracks were observed in the segment stacking yard
- I read the Feedback about this topic from Mr Charles Allen [see below] and the suggestion that the cracking of the segments as built for the project in Turkey may be due to stacking stresses. I know this project and can confirm the following additional information in efforts to be transparent in the application and success of new systems and the value to the international industry of handling the investigation of the issues clearly.
- The casting of the hybrid GFRP+MSF reinforced segments began in March 2019 and were held in the stacking yard at the factory until end of June 2019 when they started being built into the tunnel and there were no cracks observed in the segments while in the stacks.
- This application in Turkey of hybrid GFRP+MSF reinforced segments is believed to be the first in the world. During fabrication, real scale tests of the segments and the rings were conducted, in addition to all necessary materials tests, and all were positive. After the cracks appeared in the rings as built into the tunnel, further tests of the segments and the materials were carried out and all designers and engineers involved confirmed the same positive results.
- The twin tubes of the metro project in question are being excavated by TBMs supplied by two different manufacturers. Each tube has about 100m of NATM starter tunnel excavation. At TBM launch, the rings of segmental lining were erected by the vacuum segment erector of the TBM as a false tunnel in the open space, supported internally and externally, and with the annular gap in the NATM starter tunnel backfilled using the backfilling system equipped on the TBM. This is not an unusual process. It has been used at the start of TBM drives on many metro projects.
-
Ring instability issues leading to gaps and levelling problems
- The questions are, what was the quality of the ring build for the false tunnel and in the NATM start tunnel, when was the annular gap backfilled once into the NATM starter tunnel, and what was the quality of the backfilling process?
- The bolted and gasketed GFRP+MSF reinforced segmental lining comprised five segments and a key in each 1.5m wide x 300mm thick x 6m o.d. ring. The longitudinal cracks in the GFRP+MSF segments began to appear while passing through the NATM section and also once the TBM began excavating the ground and applying forward thrust to the segmental lining.
- Approximately 55 rings of GFRP+MSF reinforced segments were placed in the first tube, about 5 of them are in ground, which is safer than in the NATM section for segment loads. After segment cracks occurred in both the NATM and the ground excavation sections, the segment design and production was changed from GFRP+MSF reinforcement to traditional heavy steel rebar cage reinforcement.
-
Cracks also in steel rebar reinforced segments
- When the TBM in the second tube launched in September, the same method was used, with segments of traditional heavy steel rebar cage reinforcement of 1,100kg/ring, for the false tunnel and backfilled into the 100m long NATM starter tunnel. . . Of the 10 rings of these steel rebar cage segmental rings installed for the second tube, wide cracks, gaps and alignment problems were once again encountered. The works are ongoing with the traditionally reinforced segments and the job site is now closed to any further study of the situation pending the results of an official investigation.
- All concerns and considerations for the possible causes of the GFRP+MSF hybrid, and traditional steel rebar cage reinforced segmental lining as built, were conveyed to the contractor by the consultants and other participants of the project.
- With cracks appearing in both the rings of GFRP+MSF and traditional steel rebar reinforced segments, it is evident that the issue is concerned with the unstability of the ring build and not a fault of the reinforcement.
- From the Editor
- It takes confidence to be the first to adopt a new method, system or technique and the engineers and contractors in Turkey should be recognised for taking the bold step in the case of the world’s first use of a GFRP+MSF reinforced segmental lining. It is a setback that the application has not been successful. That, however, is no reason to cancel the development of the technique and a thorough and published investigation of the experience in will assist in understanding the situation and preparing for the way forward.
- Feedback from: Charles Allen
- In reference to potential causes for cracks appearing in segmental linings, it might simply be a case of stacking misalignment in the storage yard. If the support bearers are not in line in the segment stack, then bending moments can be induced into the segment causing it to crack.
-
- The photograph published in the reference article [repeated here], looks to be in the centre of the segment and I consider that the most likely reason for the crack is poor stacking of the segment in the storage yard or on site. This is probably the only way a crack can appear at the centre of the segment.
- The initiation of a crack is not dependent upon the reinforcement. Reinforcement only comes into play once the concrete has cracked. It is the ability of the concrete matrix alone to resist the initiation of cracks by its flexural strength.
- I think it is alarmist to start making comments, as people have, regarding poor design, bad concrete or the type of reinforcement. The only way the issue can be resolved is by a site inspection of the operational procedures, which might have been questionable.
- Best regards,
Charles Allen
Independent Consultant Engineer
UK
TBM launch in a NATM starter tunnel (left) with correct internal (top right) and external support of the false starter tunnel (below right)
Promoting macro synthetic fibre reinforcement– TunnelTalk March 2019
Fibre-reinforced concrete for precast segments – TunnelTalk May 2014
20 years of fibre concrete linings in the UK– TunnelTalk October 2010
Contract packages and boundaries
-
Article referenceTideway TBMs well into excavation – TunnelTalk September 2019
- Feedback from: Ken Spiby
-
- With regard to Fig 2 in the reference article [and repeated here], I have seen this illustration regularly and I guess it is provided by Tideway, but since when did contracts fade into one another? Is this supposed to indicate an Alliance, or that the contracts really are all fluffy at the interfaces?
- It amuses me that when graphic designers get hold of things, the original meaning can be completely lost in the quest for ‘the look’ – and no one thinks to go back to the engineers to check the illustration for accuracy.
- Best regards,
Ken Spiby
LBA, London
Connection construction underway for Tideway– TunnelTalk September 2017
Preparations to start London supersewer excavation– TunnelTalk August 2017
Funding secured for 25km London super sewer – TunnelTalk July 2015
More site investigation could have prevented Kolkata collapse
-
Article referenceKolkata TBM failure causes extensive damage – TunnelTalk September 2019
- Feedback from: Siba Prasad Sen
- With regards to the recently reported Kolkata Metro drive collapse, I believe this took place as the TBM entered a buried tidal channel running from the Ganges river, which had been filled up many decades earlier. Kolkata is built over the delta of the Ganga-Brahmaputra confluence on sand and silt and as a result, there are many such buried tidal creeks below the city.
- It is hard to accept the statement that geological investigation during planning did not indicate the presence of any water body. For such cities, geological studies are always insufficient and should be supplemented by geo-anthropological study.
- Best regards,
Siba Prasad Sen
Independent Consultant Engineer
Site investigation pays dividends on Crossrail – TunnelTalk May 2015
Core drilling for Norway’s latest mega-crossing– TunnelTalk March 2015
In search of the ideal TBM specification – TunnelTalk June 2018
Slurry or EPB for conditions in Bangalore – TunnelTalk January 2016
Tributes to Dick Robbins
-
Article referenceObituary: Dick Robbins 1933-2019
- Leaders of the international tunnelling industry speak to TunnelTalk of their recollections and remembrances of Dick Robbins as the innovator of the modern tunnel boring machines and as an industry statesman.
Lok Home, President and CEO of The Robbins Company, recalls his personal association with Dick Robbins
Jamal Rostami of the Colorado School of Mines remembers Dick Robbins and suggests a scholarship in his memory
Add your thoughts, tributes and recollections via our Feedback service or via an email.
Tributes to Enrique Fernández González
-
Article referenceObituary: Enrique Fernández González 1958-2019
- From: Jens Classen, Implenia Construction GmbH
- Tragic news.
Enrique was a well known and always helpful colleague. - From: Dean Brox, Canada
- What sad sad news.
He was a good friend since I met him at RETC Las Vegas in 2009.
A big loss for Dragados.
I will drink some good Spanish wine in his memory. - From: Pamela Moran, Schneider Moran Inc.
- Thank you for posting the Obituary for Enrique.
It was a perfect tribute and included his involvement with the CM009/CM019 contracts on the East Side Access and his instrumental contribution on the failed, but valiant, It's not over till it's under Tysons Tunnel effort together with Dr Sauer. - From: Luis Miguel Viartola Laborda, gGravity
- We feel very grateful for the Enrique’s obituary published in TunnelTalk.
- Enrique was a very especial person for all his colleagues within gGravity and Dragados. Personally, I worked with him for more than 15 years. He was a close colleague and also a true friend, besides an exceptional engineer. But he was, mainly, a good man and a family man, and will be missed in many ways.
- He was passionate, always positive, patient, and pragmatic in his work and had plenty of vision on every project he started. He had the ability to bring out the best in each person. His death has been a big loss for Dragados and gGravity, and I would want to think it is the same for the tunnelling industry.
- From gGravity we will try to continue with his legacy, and Alejandro Sanz will take his role as Head of Tunneling Technical Department. Alejandro has been part of Enrique’s team for more than 12 years, and was the person chosen by him to continue the work after his retirement. Regretably this change arrived shockingly and much sooner than expected.
- With best regards
- Luis Miguel Viartola Laborda
gGRAVITY Engineering
USA Dragados
Editor's Desk comment: Responsible management of construction materials
-
Article referencePromoting macro synthetic fibre reinforcement
- Feedback from: Des Vlietstra, USA
- In response to the Editor’s Desk comment on 7 March 2019, I find the suggestion that macro synthetic fibre is “attracting some environmental concerns” very interesting, and even a little narrow minded. Clearly there is lack of understanding of what an environmental concern is, and how an environmental concern is caused or eradicated.
- It is a little like suggesting that seafood or chicken served in restaurants is a danger to human life. If both are properly refrigerated and prepared, they pose no danger to human life. It comes down to responsible behaviour by humans.
- Macro synthetic fibre used correctly in concrete will significantly reduce the carbon which is produced by using the equivalent in steel fibre. As such, this is not an environmental concern. It is a step in the right direction.
- It is humans that dispose of macro synthetic fibre, chemicals, pharmaceuticals, oil, single-use plastic bags, batteries (and the list is endless) incorrectly or irresponsibly that pose an environmental concern. The real issue here is people. We need to take responsibility for our actions. By understanding the real problem, we can actually do something about it. Macro synthetic fibre stored correctly, or used responsibly in concrete as reinforcement, is not an environmental concern in any way.
- Best regards
Des VlietstraMSc (Eng) Advanced Concrete Technology, GDip Mining, MICT.
Technical Consultant
Barchip Inc. - From the Editor:
- The point is well madeand the Feedback links directly to the article published on TunnelTalk about the establishment of a newassociationto promote the advantages of macro synthetic fibre within the underground construction industry. Preparing industry standards, codes and guidelines for the responsible use, design and application of MSFis among the main aims of the Macro Synthetic Fibre Association MSFA. Ten of the leading manufacturers of macro synthetic fibre (MSF) arefounders of the Association whichis encouraging membership from industry and academia and will hold its next General Assembly meeting at the WTC World Tunnel Congress in Naples, Italy in early May. Contact the Association for further details.
Promoting macro synthetic fibre reinforcement– TunnelTalk March2019
Positive environmental benefits of MSF
- Feedback from: Denis Crehan
- I would like to highlight the positive environmental benefits of using more durable lower carbon footprint materials like macro synthetic fibre reinforcement instead of traditional high carbon footprint steel reinforcing options. In an industry where CO2 savings are extremely hard to achieve, a 70-80% reduction in CO2 emissions is achievable using macro synthetic fibre reinforcing compared to comparable steel mesh or steel fibre options. This helps protect our precious planet from the effects of global warming which is the number one threat to mankind on this planet.
- Reducing CO2 emissions must become the tunnelling industry number one concern. Any material that promotes lower emissions should be supported by industry clients, technical advisors and encouraged by governments through carbon taxation policy.
- See also Intergovernmental Panel on Climate Change (IPCC) report of 2018 that suggested that keeping that rise in global temperatures to below the 1.5 degrees C target would require "rapid, far-reaching and unprecedented changes in all aspects of society". Global emissions of CO2 need to decline by 45% from 2010 levels by 2030.
- Thank you
Denis Crehan
Climate control for deep metro systems
-
Article referenceRussian cities plan massive metro expansion
- Feedback from: Calvin Barrows, Chartered Engineer, UK
- I read with interest in the article about expansion of metro systems in major cities of Russia, that one of the main operating problems for the Moscow Metro is related to its ventilation system which cannot cope with the increase in temperatures during the summer season and that, due to this, Moscow authorities consider building new stations at depths currently unreasonable.
- I know the overheating statistics for the London Underground system in the UK and understand that there are a significant number of metros worldwide that are also grappling with this problem. Since the heatwave in London of 2018, I have expended some significant efforts to make my findings on the subject available and it is causing considerable interest.
- Some years ago I happened on a possible cause, partly as a London Underground passenger, and partly in my engineering role with Tube Lines Ltd, the infrastructure company at the time for London Underground Ltd. The current response to metro overheating is either to do nothing, and subject the passengers to risk and discomfort, or to install a massive plant to cool the whole of the underground network, which addresses the symptoms and not the root cause and is a totally imprudent solution, in terms of capital and running costs, and is extremely environmentally unfriendly.
- The reason for this response is, I believe, a lack of understanding of where the primary summer heat is coming from even though London Underground - the metro system I am most familiar with - has been trying to address the problem on and off for the last 100 and more years. Indeed a Cooling the Tube project commenced in 2005, but has not made any really advances in solving the overheating problem. It was more than 40°C on the London Underground Central Line last summer!
- My bold claim is that my findings and interpretation of this problem will form the basis of a solution and save billions in both cost and energy consumption worldwide. My report, published on TunnelTalk, is written deliberately as slightly light-hearted, but makes some serious points to support my theory.
- I have also reviewed reports and papers from the London South Bank University and the University of Cambridge Engineering Department on the subject and a paper by the latter entitled Thermal Modelling and Parametric Analysis of Underground Rail Systems includes the two graphs below. I was excited about discovering these because they clearly show a linear relationship between ambient temperature and temperatures underground in the tunnels and stations. My interpretation is that this supports my hypothesis, although that was not their interpretation.
-
Graphs reproduced by kind permission of the University of Cambridge Engineering Department from its paper entitled Thermal Modelling and Parametric Analysis of Underground Rail Systems
-
My interpretation is as follows:
There is consensus that underground space or non-operational railway tunnels in clay have a background temperature of about 14°C, so the model by the authors of the paper has predicted that well. However, the figures 3a and 3b show a linear relationship between the rise in ambient temperature and the rise in tunnel and station temperatures, with platform and tunnel temperatures at 17-18°C at zero degrees ambient. Hence, if we draw lines parallel to the best fit lines, which pass through the zero ambient temperature axis at 14°C, this represents a train running using zero energy to move and stop (thus producing zero heat) but with the platform and tunnel temperatures still rising linearly with the ambient temperatures. Hence, this would suggest that all the non-seasonal heat sources are accounted for in the approximate 4°C difference between the best fit line and the parallel line passing through the zero degrees ambient axis at 14°C. This makes sense because all these non-seasonal heat sources are insufficient to keep the passengers warm in the winter without supplementation from saloon heaters! - I have had a number of my engineering and scientific acquaintances review my paper and a thought that one engineer frivolously expressed was, “of course the trains know when they are just about to enter the tunnel and jettison all the absorbed heat energy whilst still on the surface” and this really helped me to focus on the bigger picture. Of course they don’t jettison their heat energy, they carry a significant amount into the tunnels and underground environment. So whilst they are on the surface we should protect them from absorbing too much irradiation by applying a sunscreen, as indeed we would for ourselves.
- I would welcome further discussion within the industry on the engaging issue.
- Kind regards,
Calvin Barrows
Chartered Engineer
UK
Borehole cooling for London Underground Green Park Station– TunnelTalk February 2012
Hong Kong-Zhuhai-Macao statistics
-
Article referenceHong Kong-Zhuhai-Macao highway sea link immersed tube construction
- Feedback from: Tommy Olsen, Denmark
- TunnelTalk, thanks for this excellent video showing construction of the Hong Kong-Zhuhai-Macao Tunnel, with many good details.
- The project was developed for Preliminary Design (for authority approval and procurement) by a JV of HPDI of CCCC (commercial lead), STEDI and COWI (technical lead) in 2008-2009 and constructed under a design-build contract by a JV of CCCC, HPDI of CCCC, FHDI of CCCC, AECOM, STEDI and COWI from 2010 to 2018. The owner HZMB, had support from TEC.
- The distance of the immersed tube, portal to portal, is 5.6km and longer if the length of the two artificial islands is included for the distance from bridge to bridge connection.
- The Hong Kong-Zhuhai-Macao undersea link is the world’s longest road immersed tunnel; the Busan-Geoje link in Korea is its deepest road immersed tunnel; the Bosporous rail link in Istanbul, Turkey is the deepest immersed tunnel; and the San Francisco Bay crossing for the BART metro system is the world’s longest immersed tunnel.
- Best regards,
Tommy Olsen
Project Manager, Tunnels at COWI
Copenhagen Area, Capital Region, Denmark
Hong Kong-Zhuhai-Macao sea link design and construction – TunnelTalk October 2018
Bosphorus rail link joins East and West – TunnelTalk October 2013
Innovations for the Fehmarnbelt tunnel option – TunnelTalk May 2010
Renewed momentum for Helsinki-Tallinn fixed link– TunnelTalk February 2018
Reflecting on Europe's first immersed tunnel – TunnelTalk March 2013
Links across the waters – TunnelTalk January 2010
Search the TunnelTalk Archive Library for news of other immersed tubes projects of the world
Impressive muck re-use on Brenner Base Tunnel
-
Article referenceUsing aggregates from tunnel excavations - TunnelTalk October 2018
- Feedback from: Philip G Graham
- Can I point out that on the Italian side of the Brenner Base Tunnel, currently under construction, this project is doing just precisely this - reusing a large portion of excavated muck as feed stock in the manufacture of the segments for two different sizes of segmental lining to be supplied to the TBM bored sections.
- On the Mules 2-3 contract the excavated muck is transported by two separate conveyor belts running parallel from the boring operations back out along the pre-existing exploratory and service tunnel between Mules and the Aica portal and on to the segment manufacturing facility at Hinteregger. From the muck storage area, a large proportion of this material will be used in the adjacent segment fabrication production.
- The completed and cured segments are conveyed by rail on a 900mm gauge construction railway back through the same exploratory and service tunnel shared with the twin conveyor belts and on up to the working faces of the TBM operations. With the imminent commencement of boring by the two main running tunnel TBMs by the end of 2018, muck reuse will ramp up to an impressive throughput on this massive project.
Linking rock mechanics to optimum TBM excavation– TunnelTalk November 2015
Brenner pushes ahead with new contracts – TunnelTalk July 2014
Brenner begins – TunnelTalk April 2011
Brenner project takes a major leap forward – TunnelTalk February 2011
Prelude to building Brenner Baseline – TunnelTalk March 2009
Semmering pilot tunnel drive – TunnelTalk February 1996
-
Article referenceBTS 2018: Video report of conference activity - TunnelTalk 11 October 2018
Our message must be clear
- Feedback from: Robinson Leon-Diaz, Associate Director Tunnels, Jacobs
- I have just seen the video regarding the BTS 2018 conference and I have left deeply concerned with a couple of statements made by two of our colleagues:
- “Tunnelling is not a science.” (0.36 on video, Raffaele Zurlo – CEO, BBT SE)
“Tunnelling is not safe.” (1.38 on video, Tomas Otterberg, Senior Product Manager, Epiroc) - I personally believe that there was a part of the message missing in translation and may the speakers have meant:
“Tunnelling is not a dark science.”
“Tunnelling is not as safe as it could be.” - I hope this is what they were intending to communicate, otherwise some housekeeping may be needed among our tunnelling community.
- Kind regards,
Robinson Leon-Diaz
Jacobs
Associate Director Tunnels
-
From the Editor’s Desk - 20 Sep 2018
- The dominance of China in the market may have hit a wall with Chinese state-owned parent of NFM declaring bankruptcy. For competitors, Chinese brands are forcing price pressures, but what about service and quality?
Chinese brand price pressures
- Feedback from: Basil Fuller, Semi-retired, Tunnel Products Australia
- The economic powerhouse that is China is about plan, plan, plan! They have the ability to deliver at a price (even though that price is subsidised), but they can also deliver quality and service. Acquisitions such as the just completed John Holland takeover, is a way of acquiring not only a foothold in the industry, but the expertise too.
- What the rest of the world needs to do is to adopt the same approach to their economy no matter how small. The lesson is focus, work hard, improve and learn.
- At the end of the day it is about the passion of the individuals to achieve, create and win. We should not be afraid of competition, but embrace the fact that it makes us think twice about it, and perhaps plan to improve.
- Best regards,
Basil Fuller
Semi Retired
Tunnel Products Australia
NFM for sale as China owner goes bankrupt – TunnelTalk September 2018
Two generations of tunnelling at Herrenknecht – TunnelTalk September 2018
Excellence in the 2018 ITA Awards shortlist – TunnelTalk August 2018
Trade fair opportunities across the globe – TunnelTalk August 2018
TBMs accepted for the Dubai stormwater drives – TunnelTalk August 2018
China Acquires Aecon of China – TunnelTalk November 2017
The rise of the Chinese manufacturers – TunnelTalk November 2016
China deal for Robbins – TunnelTalk June 2016
Leighton sells John Holland division to Chinese – TunnelTalk December 2014
-
Article referenceRefuge chamber deaths raises concerns - TunnelTalk July 2018
Use of refuge chambers in the underground works environment
- Report by: Mike Lincoln, General Manager, MineARC Africa
- While the incident in the Limpopo mine following a conveyor belt fire on Sunday 15 July does not involve a MineARC Refuge Chamber, the Palabora Mining Company (PMC) owner of the mine has developed a strong working relationship with MineARC Systems installing its first MineSAFE Refuge Chamber in 2013.
- MineARC Systems extends its heartfelt condolences to the families of those who lost their lives and to colleagues and the wider community affected by the incident. I It is particularly unfortunate that the incident occurred at a site that continues to take proactive steps in improving on-site safety and emergency response procedures.
- Since installing the first MineSAFE Refuge Chamber for PMC in 2013, MineARC Systems has since then continued to work towards establishing a safe underground environment for all personnel, with the installation of further MineARC portable chambers that are supported by a diligent service and maintenance schedule.
- Direct communication with the company indicates that the workers took refuge in a Lift 1 refuge bay supplied only with a permanent fresh air supply and with no additional life support redundancies as per the South African Department of Mineral Resources (DMR) Guidelines for Refuge Bays. Lift 2 at the Limpopo mine has three portable MineARC Refuge Chambers.
- After the conveyor belt blaze erupted, three personnel made their way to one of the permanent fresh air bays. It has been reported that the compressed air supply to the shelter was compromised affecting the positive pressure of the fresh air supply of the bay. With no sealable door, as well as a lack of any breathable air supply redundancy, gas detection or air-conditioning, a combination of overheating and smoke inhalation contributed to cause of death. High levels of CO and CO2, as well as a reading of 70°C temperatures were detected inside the fresh air bay during the rescue attempt. Unfortunately three additional workers who were unable to make their way to a fresh air bay also perished during the incident.
- It was also indicated that Lift 2 was not affected by smoke from the incident, however personnel utilised the Lift 2 MineARC Refuge Chambers for a period of time as a precautionary measure before being evacuated.
- The incident is under further DMR investigation.
- Palabora Mining Company is compliant with the current South African safety regulations. For refuge bays however, and following this incident, the company is already in the process of taking the necessary actions to avoid a similar outcome in future. This involves MineARC Systems conducting a full risk assessment of all fresh air bays on site with the aim to bring the company’s emergency response protocol (ERP) up to globally recognised safety standards.
- Sincerely,
Mike Lincoln
General Manager, MineARC Africa
Contribution to the report of the the refuge bay deaths in the South African mine
- Feedback from: Kevin Grover who withheld his industry association
- Very interesting article. Can someone please offer some thoughts on why ventilation pipes appear to have been damaged such that they fail to perform the function for which they were designed?
- Sincerely,
Kevin Grover
Integrity of ventilation in safety chamber
- Feedback from: Raymond Kryhul of the MCD Group in the UK
- All pipes that supply air to rescue chambers should be of a screwed thread type connection. The use of small bore clamped connections, with rubber seal inserts, could fail due to the heat, resulting in air loss at connection.
- With regards,
Raymond Kryhul
MCD Group, UK
Warnings for the provision and use of refuge chambers
- Feedback from: Dr Donald Lamont, Animateur of the ITA Working Group 5 on Health and Safety in Works
- It is a tragedy that three men appear to have died in a refuge chamber. There is no indication whether death was due to excessive heat or to an irrespirable atmosphere.
- Refuge chambers are complex pieces of equipment which must be equipped and operated correctly if they are to save lives. It is vitally important they are properly maintained and that all potential users are fully competent in their use. Otherwise an irrespirable atmosphere can build up in the chamber or the chamber can overheat and turn what is supposed to be a place of relative safety into a death trap.
- The ITA Report 14, Clause 1.8, recommends that persons can remain in a refuge chamber for a minimum capability of 24 hours in a standalone, i.e. self-sufficient mode. In externally supported mode, the capability is much longer as the chamber is powered and supplied from the fixed installed tunnel supply lines.
- Whilst this was a mining incident, the lessons from it should be taken on board by the tunnelling industry. The issues in question are fully covered in the ITA Report 14 Guidelines for the provision of refuge chambers in tunnels under construction.
- Sincerely,
Dr Donald Lamont
Animateur ITA WG5
Clarification of specifications for Singapore DTSS Phase 2 TBMs
-
Article referenceIn search of the ideal TBM specification - TunnelTalk June 2018
- Feedback from: Ms Woo Lai Lynn of PUB Singapore’s National Water Agency
- Dear TunnelTalk,
- We refer to the article In search of the ideal TBM specifications by Mr Lok Home published on 21 June 2018 in the Discussion Forum of TunnelTalk.
- It is mentioned in the article that there is a requirement by PUB for the TBMs used on the Deep Tunnel Sewerage System Phase 2 project to “have their main bearings changed out from inside the tunnel every 800m”.
- We wish to clarify that this statement is incorrect. Any required planned TBM main bearing change is envisaged to be carried out at intermediate shafts and not in the tunnel. There is also no requirement for bearing changes every 800m.
- Best regards
Woo Lai Lynn (Ms)
Chief Engineer (Conveyance)
DTSS 2 Department
PUB Singapore’s National Water Agency - From the Editor:
- The clarification from Ms Woo has been forwarded to Mr Home for further comment.
- Comment from Herrenknecht, as supplier of all the TBMs for the DTSS Phase 2 project (see TBM orders for Singapore DTSS Phase 2 - TunnelTalk June 2018) is that the possibility of a main bearing change from the back and within the tunnel is a standard feature of Herrenknecht machines and that the incidences of having to undertake such a bearing change is very rare with recollection of only one ever being necessary.
-
With regards,
Shani Wallis
Editor, TunnelTalk
DTSS Phase 2 TBMs - all from the same manufacturer, all but one slurry machines
-
Article referenceTBM orders for Singapore DTSS Phase 2 - TunnelTalk June 2018
- Feedback from: Richard Lewis
- It is interesting to read that all TBMs for the DTSS project in Singapore have been selected as a) supplied by Herrenknecht and b) slurry machines.
- The pros and cons of the first decision have been explored by others and in the TunnelTalk Editor’s Desk comment for this week – however the choice of using all slurry machines is interesting.
- Of course, the choice between slurry and EPB depends on many factors – the geology probably being the main one. This has been discussed and explored by many articles and papers over the years.
- Nevertheless, there are many situations where either EPB or slurry can be adopted. This is especially true in the mixed and abrasive ground which can be found in Singapore. In the past, in Singapore, EPB has often been the choice (though admittedly not always). It is a more economical TBM to purchase and does not require the space and expense of a surface slurry treatment plant.
- Often, in benign and straightforward conditions, EPB is without doubt the right choice. However in more demanding conditions of abrasive ground and perhaps greater depth, the slurry TBM option can give more security due to its greater control of face pressure and the reduced wear that it suffers. On the recently completed cable tunnels in Singapore, slurry TBMs were the choice for most, if not all, of the contracts and these were generally completed successfully. Now that slurry has been selected for almost all of the DTSS tunnels, one wonders whether it is the clients and designers in Singapore, or the contractors, that have now come to the conclusion that, in the difficult Singapore geology, the increased investment at the outset in the use of slurry TBMs, giving more security and reliability, saves cost in the long run and is the right choice in difficult and demanding conditions.
- Finally it would be interesting to know whether the decision to use all the same type and supplier of TBM was a coincidental one, made independently by all the five different contractors, or whether it was a strategic decision led by the client, while, without doubt, leaving the responsibility for the machines with the contractor.
-
With regards,
Richard Lewis, YL Associates Limited, Hong Kong
TBM orders for Mumbai Metro Line 3 – TunnelTalk February 2017
Final end to tough Bangalore TBM drives – TunnelTalk October 2016
Slurry or EPB for conditions in Bangalore – TunnelTalk January 2015
Alternative ventilation method for road tunnels
-
Article referenceTunnelTECH - An alternative air injection ventilation method - TunnelTalk December 2017
- In response to the Feedback comments from William G. Connell of WSP USA (below), the authors of the TunnelTECH paper introducing the alternative road tunnel ventilation system present the following information and make available the attached pdf
for further details. Response from Ahmad Reza Ghavami,Mechanical Engineer and CEO/Founder, Yasaman Ghavami, Project Manager, and Thomas McMahan, Marketing Specialist of Naghsh E Shahr Consulting Engineer (NSCE), Iran and USA:
- The proposed positive partial pressure (P.P.P.) ventilation system prioritizes both fire and pollutants. It can be applied for project in both modern and undeveloped countries.
- Similarities between semi transverse supply/exhaust and P.P.P. alternative:
Both inject fresh air and exhaust polluted air. - Differences between semi transverse supply/exhaust and P.P.P. alternative:
-
Semi-transverse systems
- Cost a lot of time, energy and money to construct both the semi-transverse supply ventilation system the semi-transverse exhaust ventilation system.
- Both systems require installation of ducts either in the floor or on the ceiling.
- Both systems require vents or grates to be installed to inject fresh air into the tunnel or to exhaust the polluted air out of the tunnel.
- Utilizing either of the systems requires a false floor which reduces the overall height of the tunnel.
-
Positive partial pressure (P.P.P.) ventilation system
- Reduces cost by up to one third of the traditional systems in use today.
- The only cost will be the two outside fans and the diffusers, which are installed via a duct on the ceiling of the tunnel.
- No cabling.
- Reduced maintenance inside the tunnel. No fans or cabling to require maintenance inside the tunnel, thus reducing the need to close the tunnel.
- The fans will be equipped with an INVERTOR which will allow the fans to reverse in the event of fire and high pollutants.
- The fans will be equipped with an ECONOMIZER, controlling the revolution of the fan from 0-1400 rev/min, depending on the volume of traffic in the tunnel. This accelerates or decelerate the amount of power being used by the system thus saving significantly on energy consumption costs.
- The P.P.P system uses the tunnel itself as the vehicle for moving the fresh air in and the pollutants out.
-
With regards,
Ahmad Reza Ghavami, Mechanical Engineer and CEO/Founder,
Yasaman Ghavami, Project Manager, and
Thomas McMahan, Marketing Specialist of
Naghsh E Shahr Consulting Engineer (NSCE), Iran and USA - Feedback from: William G. Connell, WSP, USA
- The paper describes a semi-transverse supply ventilation system, as noted below (Fig 1), only the delivery of air to the tunnel is at the ceiling level. This type of system has been used in many road tunnels in the past but is less common now. Fact is, semi-supply systems work best for pollutant control when air is delivered lower along the roadway at about exhaust pipe level.
- The concept is not new – but more importantly the system as described will not provide ventilation control of smoke and heat during a fire emergency which is actually the more important function of a tunnel’s ventilation system design these days. The emergency function of the system is not addressed. Because current day vehicles emit much lower levels of pollution, the critical criteria that drives the ventilation design in most modern road tunnels is the fire design criteria.
- The extra emphasis on removal of pollutants appears to suggest a filtration plant (which will not likely work due to the large volume air flows - and will unnecessarily increase fan motor horsepower). The only tunnels that I have seen using any kind of filtration system were a few in the Nordics where they were needed to help for visibility issues created by the common use of studded tires which was creating pavement dust.
- The article does not seem to account for the fan facility (building) required to house the fans at either end of the tunnel. These buildings – which will add a lot of cost – are not required for the jet fan longitudinal system being compared.
-
Regards,
William G. Connell
Assistant Vice President
Senior Technical Principal
WSP, Boston, USA - Feedback from: Petr Pospisil, Switzerland
- This system will not be efficient, as explained in the Road Tunnel Ventilation Compendium. Some designers seem to make the same errors for decades.
-
Guidelines for road tunnel ventilation
-
With regards,
Petr Pospisil,
I-P Switzerland

Fig 1. A typical semi-transverse supply ventilation system concept where air is delivered via a duct below the roadway and introduced to the tunnel at tailpipe level and is distributed with the piston effect of the traffic
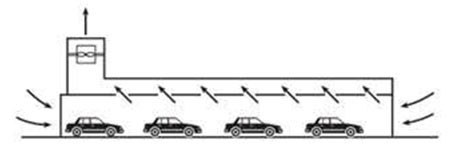
Fig 2. Design of a typical semi-transverse exhaust ventilation system concept where fresh air is drawn into the tunnel and exhausted through ports into a duct above the roadway and then discharged to ambient
Tailshield failure as source of fatal TBM collapse in Foshan, China
-
Article referenceFatal collapse of metro heading in Foshan - TunnelTalk February 2018
- Feedback from: Nick Shirlaw
- Just six months after the major tunnel collapse at Rastatt in Germany, TunnelTalk carries news of another major failure, at Foshan in China. Sadly, the Foshan failure has resulted in multiple fatalities.
- After the Rastatt failure, I noted that the ascribed cause, of failure of the tunnel lining behind the TBM, was very rare (see Feedback item below). However, there had been a (very) few other instances of the failure of segmental tunnel linings over the prior 18 years.
- The failure at Foshan is ascribed in the article to a failure of the tail seals of an EPB TBM. Again, this is a rare cause of a major loss of ground over a pressurized TBM. I know of only two other cases over the last 18 years:
1. The failure at the Langstaff Road Trunk Sewer tunnel in Toronto, Canada in 2008, which was covered in a TunnelTalk article by P Wallis in 2009
2. A loss of ground due to failure at the tail seals over one of the EPB drives for the Singapore Deep Tunnel Sewer system(1) in February 2003. Although there was a significant loss of ground, there was no injury, nor a sinkhole. Above the tunnel was the approach ramp in Singapore to the underpass where Farrer Road passes under Holland Road. The U shaped reinforced concrete approach structure settled by 48mm as a result of the loss of ground. The incident was referred to in Shirlaw and Boone (2005). - There may have been other incidents of failure at the tail seals of which I am not aware. It would be useful if TunnelTalk readers could add to the list given above.
- It is my opinion that a relatively small proportion of losses of ground over pressurized TBMs are recorded in available documentation and in professional/trade journals or newspapers. Inevitably the biggest ones are covered by the general media (as is the Foshan collapse).
- TunnelTalk is doing a sterling job of making the tunnelling community aware of many of these major incidents. However, the smaller, and, in my experience much more numerous, incidents tend to get quietly backfilled and forgotten.
- Even the bigger incidents tend to hit the headlines briefly, with only speculation as to causation. It is rare to get good forensic information at a later date. How can realistic risk assessments for pressurized TBM tunnelling be carried out if there is a fundamental lack of information on the frequency or cause of ground loss incidents?
-
Regards,
Nick Shirlaw,
Golder Associates - Shirlaw, J.N., Boone, S. (2005). The risk of very large settlements due to EPB tunnelling. 12th Australian Tunnelling Conference, Brisbane, April 2005
EPBM recovery reveals the unexpected – TunnelTalk, August 2009
Rastatt TBM drive collapse and failure of its segmental lining
Aug 2017
-
Article referencesGround freezing TBM drive collapse in Germany - TunnelTalk August 2017
Discussion Forum: Rastatt collapse raises a list of queries and concerns - TunnelTalk August 2017
Rastatt collapse raises a list of queries and concerns - TunnelTalk August 2017
- Feedback from: Rupert Sternath
- One can see out of the available publications that the segments of the lining have dislocated some 40m behind the TBM. This is an indication that the ring gap has not been filled properly. As this happened to an experienced contractor it may be the case that the grouting operation together with the TBM drive through a frozen soil includes some particular problems.
- Mining through an ice body has the characteristic of a hard rock drive, which requires some over excavation to enable shield steering.
- Most shielded TBMs use grout lines through the shield tail to fill the annual gap immediately behind the tail seal. Under hard rock conditions the mortar tends - due to the over excavation - to flow around the body of the TBM and to the front and into the working chamber and so leaving voids outside the segmental lining. These voids have to be filled by a secondary grouting operation through the segments as soon as possible from the top of one of the trailing gantries.
- In case of a frozen soil outside the gap however, it may happen that the voids are being filled by groundwater ,which would also freeze, and as heat is present inside the tunnel during the mining process, the ice in the gap may melt leaving the segments unsupported. In this case filling of the gap by blowing pea gravel through the segments combined with a cement grouting operation may be a better option in my view.
- Anyway, the tunneling world is keen to see the outcome of the following investigations and very interested on further reports in TunnelTalk about them!
-
Regards,
Rupert Sternath
Stern Consult
Holzhamer Bogen 15 83624 Otterfing - Feedback from: David Caiden
- In the discussion about the Rastatt collapse incident, mention has been made to some classic tunnel collapses and refers to precast concrete (PCC) segmental lining failures. But is it truly a “failure” in the usual sense of the word if the lining collapses under a load for which it was never designed nor intended?
- Consider this: A car gets flattened by a meteorite - would we say the body shell had “failed”? I doubt it. We would say it was “flattened by a meteorite”.
- What I am talking about here is running or flowing ground and I am reminded of the collapse in Hennessy Road during the Hong Kong Island Line construction on 1st January 1983. The hole in the rock face through which the CDG flowed under water pressure was no bigger than a fist when the flow started. But the flowing ground opened it up so much with abrading material that we ended up with a full size street lamp within the debris in the tunnel.
- My point is that flowing ground is an immensely destructive force similar to rushing floodwater. PCC linings are designed for static ground forces in the permanent cases and handling and building forces for the construction stages. They are not designed to withstand immense dynamic and changeable flowing ground forces with a battering of cobbles and other debris. The approach we take to overcome this disregarded loading case is to take measures to prevent ground flows. Naturally when these measures are unsuccessful the PCC ring will not hold up.
-
Regards,
David Caiden
Arup - Feedback from: Nick Shirlaw
- Thank you for the write-up on a major failure, which appears so far to have had limited press coverage, despite the severe impact on train operation.
- As far as I am aware, this is the fourth incidence of catastrophic segmental lining failure behind a pressurised TBM in the last eighteen years; these being:
- Hull wastewater transfer tunnel, UK [1999]
- Cairo, Egypt [2009]
- Okayama, Japan [2012]
- Rastatt, Germany [2017]
- I know of two other cases of severe, local, distortion of gasketted, concrete segmental tunnel linings, in Singapore and the USA, where total failure was avoided by providing additional support in the tunnel.
- Given the huge number of segmentally lined tunnels built over the last 18 years, the proportion that has failed is tiny; and in each case the failure has been local, without similar problems on the rest of the drive. However, the consequences of each of the failures have been catastrophic.
- To date, the best documented of the failures is that at Hull, which was the subject of an investigation that was summarised in Grose and Benton (2005)(1). Even in this case the investigation was limited and the conclusions tentative.
- The paper was the subject of a number of discussions, to which I contributed, and which elicited detailed responses that contained much additional information to that in the original paper(2). In my opinion, the conclusions were inconsistent with some of the observations made in the tunnel; I stated this in a further discussion, which was submitted, but rejected by the journal on the basis that they did not accept a second round of discussions.
- The failures at Cairo and Okayama have been the subject of a number of articles in TunnelTalk, but I have not seen any definitive explanation of causation.
- This limited response to these failures can be compared with that to the failure of the cut-and-cover tunnel at Nicoll Highway in 2004 in Singapore. This was the subject of a public inquiry, which published clear, extensive and detailed findings that have had a major effect on practice in Singapore.
- Because the failure of segmental linings is so rare, those listed above have each occurred in different countries. As far as I am aware each has been assessed in isolation. I hope that the detailed results of the investigation into the failure at Rastatt are made public, but this will take months or years, based on previous experience. Given that there have been several failures there does appear to be a case for reviewing them together, to see if there are any common features, and lessons to be learned.
- Even though these events are very rare, the consequences are so severe that we, as an industry, need to make sure that the relevant lessons are learned and the likelihood of another incident reduced.
- 1. Hull wastewater flow transfer tunnel: tunnel collapse and causation investigation, Grose and Benton, 158, October 2005, Issue GE4, Proceedings of the Institution of Civil Engineers, Geotechnical Engineering
- 2. Hull wastewater flow transfer tunnel: tunnel collapse and causation investigation, discussion report, Ground Engineering, Volume 159 Issue 2, April 2006, pp. 125-128.
-
Sincerely,
Nick Shirlaw,
Golder Associates,
Singapore
Ground freezing TBM drive collapse in Germany - TunnelTalk August 2017
Discussion Forum: Rastatt collapse raises a list of queries and concerns - TunnelTalk August 2017
Germany: Ground freezing TBM drive collapse in Germany - TunnelTalk August 2017
Japan: Five feared dead in Japanese tunnel collapse - TunnelTalk February 2012
Japan: Possible causes of Japan's fatal tunnel failure - TunnelTalk March 2012
Japan: Salvage team recovers Japan disaster TBM - TunnelTalk Sepember 2013
Egypt: Cairo Metro tunnel collapse - TunnelTalk September 2009
Simulator training for TBM operators
Oct 2017
-
Article referenceTraining the key to reducing in-tunnel incidents - TunnelTalk October 2017
- Feedback from: Valery Kogan
- It often happens that when the future operator shows brilliant theoretical knowledge, it is lost under the weight of responsibility, sitting in the operator's chair and not daring to operate the machine. All the more valuable and timely then is the offer to train operators on simulators, similar to how it is done in aviation.
-
Regards,
Valery Kogan -
Article referencesITA efforts to meet Member Nation skills gaps - TunnelTalk October 2017
Higher education and training programmes - TunnelTalk October 2017
Rockstars of tunnelling performances in Bergen - TunnelTalk October 2017
Scheduled training courses - TunnelTalk Diary Dates - Feedback from: Nick Barton
- It was good to see plenty of tunnelling education courses highlighted in your recent focus articles. I guess that beyond those organized, to a greater or lesser extent, by ITA, there are surely numerous instances of soft-ground tunnelling lectures and courses given by the International Society of Soil Mechanics.
- The International Society of Rock Mechanics and Rock Engineering (recently extended title but same ISRM acronym) has international conferences with numerous lectures on both open-face and TBM tunnelling, plus speciality conferences such as the present series referred to as TBM DiGs focusing on the operation of TBMs in difficult grounds. The third in the TBM DiGs will be in Wuhan, China, in late November 2017.
- So there are plenty of soil and rock experts ready to help try to interpret what the unpredictable ground has thrown in the way of expected tunnelling progress. And as we see from the TunnelTalk reviews of collapses, there are enough problems to keep many soil and rock consultants busy.
- Gravity never takes a rest - either in the tunnelling or medical profession - and there are all those lateral components with unwanted water pressures and poorly resisting ground. The TBM profession has yet to acknowledge the deceleration of progress rates over extending distance, as illustrated also in world record progress performances, and the link between rock quality and delays, given by a simple equation. I wonder if such points have been discussed in the numerous courses highlighted in the TunnelTalk articles.
-
With regards,
Dr Nick Barton
Courses offered by the ISRM
Oct 2017
Ground freezing TBM drive collapse in Germany - TunnelTalk, August 2017
Subsea tunnels for oilfield development - TunnelTalk, November 2013
Record drill+blast work in Norway - TunnelTalk, January 2009
Advancing the tunneling industry the Elon Musk way
May 2017
- Article references: Musk talks tunnelling concepts - TunnelTalk May 2017
- Recent reporting of Elon Musk and his vision for inspiring and spearheading technological developments in the tunnelling industry has generated several points of Feedback, from support and agreement to points in principle, to notes on fact checking.
- Feedback from: James Wonneberg, Co-Founder & CEO, GraphicSchedule.com
- Elon Musk’s interest in tunneling is not new. In fact, he has been talking about the need for 3D networks of tunnels for years. I have always found him and his proposals and ideas fascinating, and check his Twitter account regularly for updates. So I was thrilled when he announced his intention to “build a tunnel boring machine and just start digging”.
- Those who follow along, know that Musk’s tweets are carefully worded announcements that carry a lot of weight. I knew right away that our industry could soon be swept forward with the same rapid acceleration that the automobile and space industries have felt already, fueled by one of the greatest innovators of our time. For a glimpse into how Musk and his companies operate, pick up a copy of Elon Musk: Tesla, SpaceX, and the Quest for a Fantastic Future by Ashlee Vance. It is a dynamite read.
- Right after the initial tweet on 17 December 2016, I started working my network to try to make contact. My thinking was, basically, I work on tunnels…surely Musk will need my help to put a plan together. (Ha!) A friend of mine in Silicon Valley eventually found the guy at SpaceX leading this effort, and reached out to introduce me via email. To my surprise, he responded. Amazing! We connected for a quick phone call – and I mean quick. He spoke lightning fast, which, it turns out, is how Musk's companies do just about everything.
- We exchanged some rapid-fire questions about their mission, then he informed me that they planned to break ground on the entry shaft within a few weeks (check) and expect to be digging tunnel within a few months (believe it). As we have heard in Musk’s remarks at the recent TED conference in Vancouver, he wants to improve tunneling speed by 500% to 1,000%, which will make the underground more accessible for all sorts of infrastructure.
- You see, these guys are not waiting around for industry roundtable discussions, feasibility studies, and the like. They are tackling this from a completely different ‘first principles’ angle and approach. Count me in the camp that believes this sort of thinking will have a very positive impact on this great profession of ours. It saddens me when industry giants scoff and shake their head in unison about Musk’s chances of success. But this reflects more on our own imagination than it does on the innovator himself. For sure there will be bumps along the way, but - given his track record – who is going to bet against Musk?
- Tunneling on Mars, anyone? James Wonneberg
- Feedback from: Lok Home, President, The Robbins Company, from the company website blog
- “I was inspired to write for the company blog following announcement that Elon Musk is entering our business—the tunnel boring business. It is great to see people with a vision of an improved world enter our industry. I agree with Musk that the advance rate of tunnels can be significantly improved if development money comes into the industry. Development money in tunneling, however, is at best minimal and is more often essentially non-existent. Nearly all tunnels are heavily specified to avoid risk taking by owners (therefore discouraging new development). Nearly all tunnels go to the lowest bidder and low bidders try to buy the TBMs at the lowest price; a further discouragement of development. The industry has therefore been slow to improve advance rates, but with Musk bringing the issue into the spotlight, perhaps things will change.” Lok Home
- Feedback from: Retired tunnelling engineer in the UK
- “I have always considered that we could and should be achieving a kilometer a week in advance rates. Lining operations slow up progress but techniques could be developed for using the minerals in the earth itself to create the tunnel lining in-situ – methods of vitrifying the walls of the tunnel behind the advancing TBM for example.”
- TunnelTalk in reply: Back in the early 1980s, at the height of the ‘cold war’ with what was then the USSR, a notion was circulated among tunnelling engineers that the Soviet Union was using nuclear detonations to create the massive caverns needed to house hydropower plants and military arsenal bunkers. NASA in the United States funded a project to know if operation of a TBM, working through hard rock, could be detected by satellites. The proposal was to use TBMs to excavate as-needed missile silos, rather than have them pre-excavated and equipped to house missiles in readiness. The results of the study are unknown at this moment and collapse of the Soviet Union regime superseded the need for self-excavation of missile launching silos.
Co-Founder & CEO
GraphicSchedule.com
President
The Robbins Company
Fact checking re cost of Los Angeles Metro construction
- TunnelTalk Editor: In his TED interview at the Vancouver conference, (and as published on TunnelTalk), Musk answers the suggestion that tunnels are expensive to build by stating as an example that a “LA subway extension, which is 2.5 miles long, was just completed for $2 billion.”
- On checking the facts, it is difficult to understand which of the Los Angeles Metro projects he is referring to.
- Of recent Metro projects, the Gold Line, is the most recently completed addition to the network. The new 6-mile extension with eight stations into East Los Angeles is mostly at grade, with a 2-mile section of twin tube running tunnels and two underground stations beneath Boyle Heights. It was completed and opened to service in November 2009 at a civil construction contract cost of US$600 million (about $300 million for the underground works) and a total project cost of US$898 million. An average of $166 million per mile.
- The Crenshaw-LAX Line, which is currently in construction is 8.5-miles long $2.058 billion project and is also mostly at grade with a maximum 1.9-miles in bored tunnel to link three underground stations. It is scheduled to go into service in 2019 and is being constructed for a total construction cost of US$1.3 billion including M&E installations. An average of about $238 million per mile.
- The Regional Connector in Downtown Los Angeles, to connect the Metro Blue, Gold and Green Lines is 1.9 miles long, has three new underground stations and comprises sections of open cut work, twin tube TBM bored tunnels and a SEM crossover structure. It is being constructed for a total US$927.2 million and is scheduled to open for service in 2020. Less than $500 million per mile.
- The Purple Line Extension along Wilshire Boulevard to Westwood is a 9-mile long, all underground, twin-tube TBM bored running tunnel project with seven cut-and-cover underground stations, and has a forecast estimated construction cost of US$6.3 billion. This is an estimaded average of about $700 million per mile.
- Its construction is divided into three stages.
- Stage 1 is 3.9 mile and includes three underground stations. Construction started in November 2014 and the design-build construction contract for the twin tube tunnels and the underground station civil works was awarded for a total of $1.636 billion. The total estimated $2.821 billion section is due to open in 2023. About $770 million per mile.
- Design-build construction of Stage 2 of the project, at 2.62 miles and with two underground stations, was awarded in February 2017 for a civil works contract price of US$1.37 billion. It is due to open in 2026. About $523 million per mile.
- The third and final State 3 of the current Purple Line Extension project to Westwood is 2.48 miles long and has two underground stations. Its civil works contract is yet to be tendered.
Design and performance of cast-in gasket discussion continues
Feb 2017
- Article reference: New technology to avoid segment cracking - TunnelTalk February 2017
- In response from Steve Casey, B.Sc MIMMM C.Eng, Sales & Technical Director, VIP to the Feedback contribution below from Peter Tiedemann of Dätwyler:
- VIP recognises Dätwyler as a longstanding manufacturer of high quality tunnel segment gaskets. Both our organisations have made significant contributions in the development of high performance tunnel segment gasket design and manufacture. In response to Peter’s comments, we would like to clarify the following.
- VIP cast-in tunnel segment gaskets, created using the technology outlined in the original TunnelTECH Modern seals for segment lining integrity article on TunnelTalk in May 2016, do not have ‘soft corners’. The advantage of the VIP approach is that the corner performance in terms of compressibility is consistent with the rest of the gasket, with proven sealing performance as demonstrated in recent contracts secured by VIP.
- Using solid corners, by definition, exhibit a different compression behavior, compared to the rest of the gasket, and may lead to performance issues. The ability to create a gasket corner angle equal to that of the segment, as opposed to ‘forcing’ a solid right angle corner to work on acute or obtuse segment corners, is self-evidently a better option. The inventive steps in the VIP gasket fabrication process, relates to how the extruded lengths of gasket are joined to form the gasket corners. This unique process is the result of the development work VIP has undertaken, which requires bespoke manufacturing equipment exclusive to VIP.
- Steve Casey, B.Sc MIMMM C.Eng,
Sales & Technical Director, VIP Polymers - The debate concerning the design and performance of cast-in sealing gaskets for tunnel lining segments continues with feedback on a VIP Polymer News Release article published on TunnelTalk from Peter Tiedemann of competitive gasket supplier Dätwyler.
- Tiedemann contends that producing “soft corner is easy, but [the design] has no water tightness performance. The importance is to find the balance of a strong corner with high water tightness performance and in consideration with concrete strength and other parameters.”
- He adds that: “The cutting [technique] mentioned is done already for years” and that “if doing it now, then they are years behind”.
- The track record for the design, manufacture, production and application of cast-in segmental lining gaskets is relatively limited but growing steadily. The topics were discussed in the Modern seals for segment lining integrity TunnelTECH article on TunnelTalk in May 2016.
- Share your comments and experiences of researching or working with the technique via our Feedback facility.
Modern seals for segment lining integrity - TunnelTalk May 2016
Considering the real costs of driving TBMs into predictably difficult situations
- Article reference: TBM rescue for Tapovan hydro challenge - TunnelTalk December 2016
- Feedback from: Dr Nick Barton
-
Dear TunnelTalk,
Maybe those contemplating long TBM drives into predictably difficult conditions should consider the time delays likely to be incurred for dealing with fault zones, and the deceleration of TBM progress as the drive advances. These two realities are, and have been, largely ignored by the industry these last 15 years. - My lecture for the ISRM (International Society for Rock Mechanics), entitled TBM Performance: From Best to Not So Good and Why, addresses these issues squarely and may be of interest to your readers.
-
With regards,
Dr Nick Barton
ISRM lecture by Dr Nick Barton - ISRM, September 2015
(Note: Lecture begins at 04.50 after the introduction)
Freeing stricken TBMs in tough Asian conditions - TunnelTalk, March 2012
Subsea tunnels for oilfield development - TunnelTalk, November 2013
Rail-bound support on the Doha Metro
Aug 2016
- Article reference: Doha Metro set for final project breakthrough - TunnelTalk August 2016
- Feedback from: Philip G Graham Retired, Tasmania, Australia
-
Dear TunnelTalk,
I would like to point out that not all the Doha projects used the pneumatic-tyred multi-service vehicles sourced from the various subsidiaries of the TBM manufacturer nor did they all use continuous conveyor mucking systems. -
Rail-bound mucking on Red Line South
- I endeavor to follow the products of the rail-based construction suppliers and in the case for the Red Line South (RLS) Package 2, the contractor, the Qatari Diar/Vinci (QDVC JV)/GS Engineering/Al-Darwish grouping used rail bound systems including locomotives supplied by SCHÖMA of Germany and rolling stock supplied by Mining Equipment Ltd of the USA. Mucking out over this section was achieved using rail-mounted lift-off muck cars. I note that the tunneling on this section was the first to start boring.
- This illustration shows the Schöma CHL350-BB diesel-hydrostatic locomotive paired with a powered platform car, also hydrostatically-driven from the locomotive, and contributing to the tractive force utilizing the weight of the lift-off muck car it carries. The balance of the rolling stock rake consists of the slightly larger hauled muck bins.
- The Package 1 Red Line North (RLN) contractor, the Salini-Impregilo/SK Engineering/Galfar Al Misnad grouping also used rail-based equipment for their section of the project. At some stage it might be interesting to look at the types of equipment used in the back-up systems supporting the major TBM manufactures\types.
- The recent trends towards using the pneumatic-tyred multi-service vehicles have limitations dictated by tunnel diameter of a minimum of 6~7m in the metro tunnels. Below this it is still usually the preserve of rail-bound rolling stock for excavation support. Above this, it is optional with some contractors still electing to continue with rail-based equipment.
-
Philip G Graham
Tasmania - retired
Adding to the decompression discussion
Dec 2015
- Article reference: Experience with German decompression tables - TunnelTalk Dec 2015
- Feedback from: Dr Donald Lamont C.Eng, FICE, Director, Hyperbaric and Tunnel Safety Ltd, UK
-
Dear TunnelTalk,
I very much welcome the article by Assenmacher and Förster on the use of German decompression tables. Whilst the decompression outcome on individual contracts can sometimes be found in the literature, there is little published information on national experience. It is particularly interesting having the authors’ views on the practical issues surrounding compressed air working in accordance with German practice and to realise how similar their experience has been in many ways to my UK experience. - As the authors note, oxygen decompression has become mandatory in many European countries over the past two decades. Although the UK Blackpool Tables with oxygen is the approved decompression regime in the UK, most of what little compressed air work has been undertaken in the last 15 years in the UK, has been done using variants of the German tables. Contractors prefer the shorter more aggressive decompression to the longer slower decompression of the Blackpool Tables. The UK HSE (Health and Safety Executive) Research Report RR126 found that, of the European oxygen decompression tables modelled, no one table was best or worst overall.
- With one or two exceptions, the decompression outcomes reported from the use of German oxygen tables appear generally good, for which the authors should be congratulated.
- The results for the Lübeck Tunnel, at a decompression illness incidence of around 2%, in the pressure range 1.8 to 3.1 bar, is consistent with UK figures for the Blackpool Tables without oxygen.
- In reviewing the factors that appear to affect decompression outcomes, the authors mention the problems of lack of working space. In the days of hand tunnelling in compressed air, with many weeks of man exposures, the manlocks were often fairly large and relatively spacious, particularly if they were combined man-material locks. The men could walk around during decompression. Although seating was often provided, it was usually fairly spartan or rudimentary. Now, with TBM locks, there is a lack of space in the manlocks leading to poor posture and inability to move or even to stretch the legs. In drafting EN 12110 we were certainly acutely aware of the need to balance the space requirements of those being decompressed, with the space constraints in modern TBMs.
- The problem of posture, which the authors identify, is also familiar. This was not restricted to TBM airlocks. Comments in the lock attendant’s register to report that an operative “fell asleep with arm against chamber wall” were not uncommon against entries recording Type 1 decompression illness in a miner’s arm.
- I also recognise the issue of forced posture, especially kneeling, leading to decompression illness events. The problem, in my experience, seemed to occur particularly with fitters and electricians when major failures of pumps and motors occurred, leading to urgent extended maintenance work. I routinely met with the contract medical adviser at the end of a contract to go through the compressed air working data and try to find reasons for decompression illness events.
- On the issue of acclimatisation, I have changed my opinion over the years. The pattern of compressed air working has changed with the increased use of TBMs. We have moved from daily exposures for months on end, to intermittent exposures which can be on a weekly or even monthly basis.
- Acclimatisation was described by Paton and Walder in their 1954 paper(1). They observed the same group of miners over a period of days, from the start of a contract, and noticed that the daily incidence of decompression illness reduced over time. They considered that observation to be evidence of acclimatisation. In my analysis of UK decompression illness records, I observed a similar effect in groups of miners who had all experienced multiple decompress illness events on UK contracts between 1984 and 2001. However, if acclimatisation exists, then the effect should be demonstrable in both groups and individuals. I postulated that the effect of acclimatisation on individuals should mean that, for persons with multiple decompression illness hits on the same contract, it would be possible to demonstrate longer intervals between successive decompression illness events. I looked at the individual miners on the assumption that acclimatisation would make them less susceptible to decompression illness, and hence increase the time between subsequent decompression illness events, and could find no evidence to support my hypothesis that individuals could become acclimatised.
- Of particular interest is the conclusion by the authors that a major reason for a change in the incidence of decompression illness in 2006 was the more flexible application of the tables. The ad-hoc introduction on site of “factors”, has been a feature of decompression procedures in tunnelling for many decades but often went unreported. The ‘one table higher and/or one pressure increment longer’ approach has been used, effectively, as a way of making up for deficiencies in the tables, leading to more acceptable decompression illness incidents. Being aware of such adjustments is very important when analysing or comparing the effectiveness of different tables.
- Although the authors, in their symptoms and findings, mention incorrect behaviour by the workers, I wonder whether we should accept that their behaviour is not ‘incorrect’ but ‘normal’ and make adjustments accordingly in the tables.
- In looking at the authors’ conclusions, I recognise and agree with most of them, however I wonder if ‘adaptations’ and ‘time surcharges’ is the way forward, or whether more conservative tables are required which take better account of deficiencies in the behaviour of the humans involved. After all, we now have the mathematical modelling capability to predict the likely outcome from any given decompression profile, and, with the use of post-decompression monitoring, we are able to link outcome with prediction and hence reduce the risk of decompression illness in the workforce.
-
With regards,
Dr Donald Lamont C.Eng, FICE
Director, Hyperbaric and Tunnel Safety Ltd, UK - 1. Paton W.D.M. and Walder D.N. (1954) Compressed Air Illness An Investigation during the Construction of the Tyne Tunnel 1948-50, Special Report Series No 281, London, Medical Research Council
Donald Lamont is a member of the CEN/TC151/Working Group 4 committee responsible for drafting European standard EN 12110 on Airlocks – safety. He is a member of the Compressed Air Working Group of the British Tunnelling Society (BTS) and is Animateur of the ITA Working Group 5 on Health and Safety in Works. As a member of both, Lamont led the publication of the joint BTS/ITA Compressed Air Working Group Guidelines for good working practice in high pressure compressed air
Correcting the record of the first EPBM operation in the USA
Sep 2015
- Article references: From the Archive: Anacostia challenges America's first EPBM - TunnelTalk March 1987
- Feedback from: Pete Petrofsky
- One has to be careful in making a claim of first of anything.
- In the case of first use of an EPBM in the USA, the actual first use of an EPBM was by Obayashi on the San Francisco North Shore Outfalls Consolidation Contract N-2 in 1979. This was a 3.7m o.d. Mitsubishi machine working through wet silts and sands under North Point Street in the Fisherman's Wharf area. The bidding documents allowed use of either a TBM or compressed air, with temporary support to be designed by the contractor and I helped Obayashi with their bid by producing estimates for the alternatives that clearly showed the savings in using an EPBM.
- Their bid easily won the contract and left their American competitors thinking they had "bought the job" to gain a foothold in the USA. In fact, they made a profit on the job and opened a few eyes to this new technology for tunnels in wet soils.
- The lining design was a relatively light bent steel plate type designed by the late Jim Wilton, my partner at Jacobs Associates. My memory is that progress averaged about 60ft/day.
- Feedback from: Victor Romero
- Dear TunnelTalk: Your Archive article on the WMATA Green Line crossing of the Anacostia River in 1987 was very interesting and highlighted what a great achievement that project was for all involved.
- Such acknowledgment is also deserved by the North Outfall Consolidation Sewer N-2 Tunnel in San Francisco, which was completed in 1980 by Obayashi with a TBM supplied by Mitsubishi. This project can be recognized as the first use of EPB technology in the United States. An excellent paper on the N-2 project was authored by Clough, Sweeney and Finno in 1983 in the Journal of Geotechnical Engineering.
- Feedback from: Russell Clough
- I believe the first EPB in the US was the Mitsubishi machine on Obayashi's N-2 project in San Francisco in 1979-1981. This was some six years before the Anacostia crossing project in Washington DC.
- Obayashi was low bidder on two projects in San Francisco (N-1 and N-2) and they asked me to be Project Manager on both jobs. Tunnels & Tunneling did an article about that particular management choice that featured Mr Obayashi on the cover and quoted him as asking Joe Casey the President of Dillingham if it was okay to hire me.
- N-1 was a Mitsui roadheader excavation operation with ribs and boards for immediate support while the N-2 contract was based on an EPB operation using steel liners. If you go back into the T&T archive you will find several articles about the jobs.
- Both tunnels were about 12ft diameter excavated and I recall Richard Lovat asked me if he could visit the job and I took him in on night shift in order not to disturb the OG people who did not realize that this was common practice in the States (I believe that was the first EPB Richard had seen).
- Several years after the jobs were completed and all the controversy was settled, the OG people honored me with a special awards dinner and I believe we all have great respect for the first EPB job in North America. The Japanese equipment engineers and contract managers etc were excellent and the American workers performed well.
Personal thoughts on the application of mega-TBMs
Apr 2015
- Article references: Discussion Forum: Reflections on the Alaskan Way mega-drive - TunnelTalk Apr 2015
- Yes for decades TBMs and a few digger shields have had similar problems as those being experienced currently on the SR99 TBM project in Seattle. That is why it is so SAD to see what highway engineers are doing for tunnels in Seattle and Los Angeles, thinking: “I can run a dozer. TBMs are not much different.”
- In 1985, I was assisting the first underground railway in Guangzhou, China for the heavy rail subway. French engineers wanted to give them a 25ft diameter enclosed face shield. I told them as long as it is free and to ask for 10 spares for anything made of rubber, plastic, and flexible piping.
- Bertha probably had an equipment and operator error. It is called torque for a 60/30ft lever arm. Probably no pressure gauges in the TBM to measure torque or the 1% change in face alignment or the operator wasn’t watching and no on-board CAO system was in place, operating, or being read. With torque, seals, gaskets, and bearing crash. This isn’t rocket science. TBMs have been operating since 1982 or before.
- I prefer open face mining like the 2014 completion of Caldecott fourth bore highway tunnel and the Devil’s Slide highway tunnel in the San Francisco Bay Area in California. No TBM problems.
- Bertha's problems are applicable for comments in California where the Los Angeles SR-710 DEIR [draft environmental impact report] is proposing four (4) 60ft diameter TBMs to meet at 2 miles in. No inventory of abandoned water wells has been conducted. Many homes in the 1900-1930 period may have had their own water wells for irrigation. Sometimes they used steel pipes for casing the wells and most drillers of the period would use standard oil field technology – up to about 300ft deep – and including 8in steel pipes. If abandoned they would normally dump cement and sand down the hole. If Big Hilda TBM ran into such a pipe without proper pressure monitoring – poor Hilda stuck again – we told you so!
-
Dr Tom Williams
USA
Exploring the development of embedded liners on tunnel lining segments
Nov 2014
- Article references: First use of embedded line in tunnel segments - TunnelCast video, Oct 2009
- Dear TunnelTalk,
- I was interested in the video article on your latest TunnelTalk Alert entitled First use of embedded liner in segment.
- It describes the first use of a plastic liner fixed to the precast concrete segments during their fabrication which was developed for the Sacramento Upper Northwest sewer project in Northern California and managed during installation by Project Manager on site, Pat Doig, for Construction Management team Hatch Mott MacDonald for the owner, Sacramento Regional County Sanitation District.
- Although it is the first use of an embedded plastic liner on precast concrete segments, as a matter of historical interest, it is not the first use of an embedded liner on concrete segments.
- An earlier use was for the second Dartford road tunnel under the Thames in the UK that was built by Balfour Beatty in the 1970s and with Mott MacDonald as the project engineer and designer.
- In that case it was a steel liner attached to the precast concrete segments by steel fishtails. Steel strips were then welded over the joints to make the lining watertight. Unfortunately the water pressure got behind the liner and in some places pushed it off the concrete segments, with the result that the tunnel started to leak in some places. As far as I know it was never used again.
-
Best regards,
Alastair Biggart,
UK Tunnelling Consultant - From the Editor: For those who have access to a print magazine archive, construction of the second Darford road tunnel was the topic of an article by Piers G Harding in the Jan/Feb 1997 issue of Tunnel&Tunnelling, the official magazine of the BTS-British Tunnelling Society
Response to macro-synthetic fibre critique
Nov 2014
- Article references: Critique of synthetic-fiber FRS paper - TunnelTalk, September 2014
- From Dr Stefan Bernard, TSE Laboratory, Australia
- Dear TunnelTalk,
-
Thank you for providing me the opportunity to respond to the recent criticism published in TunnelTalk by Mr Pierre Rossi[1] as Critique of synthetic-fiber FRS paper. The criticism concerned a paper I published at the WTC 2014 conference at Iguassu Falls in Brazil in May 2014[2]. The original article is titled The Use of Macro-synthetic FRS for Safe Underground Hard Rock Support but unfortunately was not included with the criticism thereby making assessment by others somewhat difficult. I would like to respond to the criticisms levelled against that paper through the following series of points.
-
The article by Mr Rossi comes as no surprise given that he has published previous papers promoting steel fibres[3] and is a consultant to Bekaert. His criticisms essentially mirror the stock standard arguments that steel fibre manufacturers have promoted for many years. However, there appears to be a discontinuity between the theory Mr Rossi likes to base his criticisms upon and reality, given that several million m3of macro-synthetic fibre reinforced shotcrete (MSFRS) is now successfully performing its role as ground support in underground hard rock excavations around the world, with a further 1.5 million m3 being added annually. In addition, recent civil tunnels in Norway have seen macro-synthetic fibres used in more than 80% of the shotcrete used for ground support, with the remainder comprising steel fibres or rebar. The great success that macro-synthetic FRS has enjoyed internationally suggests the basis of the steel fibre industry's arguments against macro-synthetic FRS needs revision.
-
As noted in my paper at the WTC 2014, the main drivers for the adoption of macro-synthetic fibres as reinforcement in shotcrete for hard rock support have been its demonstrated performance in the field, together with economic and corrosion-based advantages over steel fibre reinforcement. Its effectiveness in the field has defied the many naysayers who fret about alleged creep problems. The simple fact is that engineers employed in the hundreds of mines and civil tunnels internationally that now use MSFRS do not care what material the reinforcement is made of provided it performs the roles required of it. But unlike engineers in the field, advocates for steel fibres prefer to rely on theory as a basis for claims against macro-synthetics rather than actual performance in the field. Numerous papers have also been published on the problems steel FRS has exhibited in relation to corrosion at cracks or embrittlement in concrete of 40MPa 28 day strength and upwards[4-9], yet these studies are conveniently ignored.
- In relation to technical criticisms, one can firstly ignore the comments about 'retaining walls' and 'ductility in the interior of cracks' since neither of these topics was mentioned in the WTC 2014 paper. However, Mr Rossi made the following explicit claim in relation to macro-synthetic FRS:
-
"With this type of fiber reinforced concrete, the only way to ensure the stress hardening behaviour of the material, and therefore to permit redistribution of forces, is to have a hyperstatic mechanical system. This is the case when the underground support interacts with rocky ground with hard rocks."
-
This passage implies that 'stress-hardening behaviour' is a requirement for shotcrete to perform successfully as ground support in hard rock applications. I challenge anyone to point out an example of the successful use of a 'stress hardening' FRS anywhere in the world! One of the most successful and widely used approaches to the design of ground support with FRS is the Q-system[10, 11], which has been shown to work very effectively with strain-softening FRS exhibiting an energy absorption of only 1,000 Joules at 25mm deflection in the EN14488.5 square panel test[12] (or 400 Joules at 40mm deflection in the ASTM C1550 round panel test[13]). There is no requirement for stress hardening behaviour in this or any other widely used design method for hard rock FRS linings. This is one of the reasons why dosages of macro-synthetic fibres are seldom required to exceed 7kg/m3, and steel fibre dosages seldom exceed 40kg/m3, to achieve satisfactory support of hard rock. In shotcrete there is a diminishing return in post-crack performance as fibre dosage increases since fibre rebound increases rapidly as dosages exceed the levels indicated above. Dosages of 50-60kg/m3 of steel fibres are also exceedingly difficult to spray, which anyone familiar with fibre reinforced shotcrete would know.
- On embrittlement (or post-crack performance loss with age), Mr Rossi says:
-
"I assert that the steel fibers usually used in shotcrete, having a length of around 30mm, can be used in a matrix for which compressive strength can reach 90MPa with only a small percentage of them breaking."
-
This unsubstantiated claim flies in the face of numerous experimental studies conducted on both shotcrete and cast FRC with steel fibres, incorporating thousands of test specimens, including recent research published at the WTC 2014 in Brazil[9], an international symposium on shotcrete held in Norway in June 2014[8], and a tunnelling conference held in Sydney in September 2014[7]. One has to ask the question: how many times does the same investigation have to be performed, resulting in the same damaging outcome, before the reality is accepted that steel FRC loses performance with age? The continued denial by the steel fibre industry of the insidious problem of performance loss with age reminds me of the tobacco industry's response to lung cancer in the 1970s.
-
In relation to corrosion, I agree with Mr Rossi's claim that the small diameter of steel fibres means that disruption of the concrete matrix is minimal when corrosion occurs. However, the small diameter also means that only a shallow degree of surface corrosion is required before substantial loss of fibre cross-section occurs, leading to rapid loss of structural capacity at cracks, as demonstrated by Kaufmann in his recent research performed in Switzerland[9], and Nordstrom in earlier work performed in Sweden[14]. It merely needs to be pointed out that ground water leaks through shotcrete tunnel linings in road tunnels or metro tunnels are widely observed and evident to most members of the travelling public. Cracks can therefore allow water to pass through a lining directly to exposed fibres at a crack. The claim that cracks in shotcrete linings heal themselves and are therefore nothing to worry about is commercially-driven wishful thinking. Pressure gradients give rise to transport of oxygen and aggressive agents directly to steel fibres at cracks rather than via slow diffusion-based transport mechanisms. This is why corrosion occurs much faster in real tunnels than in lab tests.
-
In relation to creep, users of steel fibres remain constrained by crack widths to 0.30mm or less because of concerns about corrosion of steel and mistakenly assume the same constraints apply to MSFRS. These concerns are misplaced because there is no steel in a MSFRS lining, and thus there is no need for crack width limits related to corrosion. Use of macro-synthetic FRS is a 'liberation' from the constraints implied by the use of old corrosion-sensitive technology like steel reinforcement. The underground mining industry discovered this many years ago and has consigned steel fibres and mesh to the dustbin of 'technologies we no longer need's[15]! The more conservative civil tunnelling industry is taking longer to come to the same conclusion but is clearly moving in the same direction as evidenced by the increasing number of civil tunnels using MSFRS in preference to steel reinforcement[16, 17].
- In summary, the criticisms levelled by Mr Rossi represent the viewpoint of steel fibre advocates that are primarily based on theoretical arguments against macro-synthetic fibres that do not match the reality seen in hard rock ground support internationally. The reason for this reliance on theoretical arguments is that these same advocates cannot point to any actual tunnels lined with MSFRS that have suffered distress in the form of excessive convergence or any other form of unsatisfactory in-service performance of the type they have frequently claimed will happen. To the contrary, macro synthetic FRS has performed very well, justifying its near universal adoption in underground mining in countries such as Australia, and rapidly advancing adoption elsewhere[15]. Steel fibres were an advance over alternatives when they first emerged commercially in the 1970s, but macro-synthetics represent a further advance in fibre technology by providing complete protection against corrosion and other serviceability-related concerns.
-
Regards,
Dr Stefan Bernard
- 1. Critique of synthetic-fiber FRS paper – TunnelTalk, September 2014
- 2. Bernard, E.S. The Use of Macro-synthetic FRS for Safe Underground Hard Rock Support, World Tunnelling Congress 2014, (Edited by Negro, Cecilio and Bilfinger), Iguassu Falls Brazil, p40.
- 3. Rossi, P. Steel Fibres or Synthetic Fibres?, – Tunnels & Tunnelling, July 2009
- 4. Banthia, N. & Trottier, J-F, 1994. Concrete Reinforced with Deformed Steel Fibers, Part 1: Bond-Slip Mechanisms, ACI Materials Journal, Vol. 91, No. 5, Sept-Oct, pp 435-446.
- 5. Bernard, E.S. & Hanke, S.A., 2002. Age-Dependent Behaviour in Fibre Reinforced Shotcrete, Fourth International Symposium on Sprayed Concrete, Davos, Switzerland, 22-26 September, pp11-25.
- 6. Bernard, E.S. 2008. Embrittlement of Fiber Reinforced Shotcrete, Shotcrete, Vol. 10, No. 3, pp16-21, American Shotcrete Association
- 7. Bernard, E.S., 2014. Age-dependent Changes in Post-cracking Performance of Fibre-Reinforced Concrete for Tunnel Segments, 15th Australian Tunnelling Conference 2014, Sydney, 17-19 September, pp229-235.
- 8. Bjontegaard, O., Myren, S.A., Klemtsrud, K., and Kompen, R., 2014. Fibre Reinforced Sprayed Concrete (FRSC): Energy Absorption Capacity from 2 Days Age to One Year, Seventh International Symposium on Sprayed Concrete, Sandefjord, Norway, 16-19 June, pp 88-97.
- 9. Kaufmann, J.P., 2014. Durability performance of fiber reinforced shotcrete in aggressive environment, World Tunnelling Congress 2014, (Edited by Negro, Cecilio and Bilfinger), Iguassu Falls Brazil, p279.
- 10. Barton, N. & Grimstad, E. 2004. The Q-system following thirty years of development and application in tunnelling projects, Rock Engineering - Theory and Practice, Proceedings of the ISRM Regional Symposium EUROCK 2004, Salzburg, Austria, pp. 15-18
- 11. Barton, N., 2012. Defining NMT as part of the NATM SCL debate – TunnelTalk, September 2012
- 12. BBS-EN 14488, 2006, Testing Sprayed Concrete, British Standards Institute, London
- 13. ASTM International, C1550, Standard Test Method for Flexural Toughness of Fiber Reinforced Concrete (Using Centrally Loaded Round Panel), ASTM International, West Conshohocken, 2012
- 14. Nordström, E., 2001. Durability of steel fibre reinforced shotcrete with regard to corrosion, Shotcrete: Engineering Developments, (Edited by Bernard), pp213-217, Swets & Zeitlinger, Lisse
- 15. Bernard,E.S., Clements, M.J.K, Duffield, S.B., and Morgan, D.R., 2014. Development of Macro-synthetic Fibre Reinforced Shotcrete in Australia, Seventh International Symposium on Sprayed Concrete for Underground Use, June 16-19, Sandefjord, Norway.
- 16. Decker, J.B., Madsen, P.H., Gall, V, and O’Brien, T.M., 2012. Use of Synthetic, Fiber-Reinforced, Initial Shotcrete Lining at Devil’s Slide Tunnel Project in California, Transportation Research Record: Journal of the Transportation Research Board, No. 2313, pp. 147-154.
- 17. Gonzalez, M., Kitson, M., Mares, D., Muir, M., Nye, E., and Schroeter, T., 2014. The North Stratfield Rail Underpass – Driven Tunnel Design and Construction, 15th Australian Tunnelling Conference, Sydney, pp369-374.
The cons for having all the TBM delivery eggs in one basket
Mar 2014
-
Article references:
Soft ground challenge for Doha EPBMs - TunnelTalk, February 2014
Herrenknecht sweeps Doha Metro Phase 1 - TunnelTalk, January 2014
Weekly Alert Editor's Desk Comment - TunnelTalk, 27 February 2014 - Dear TunnelTalk,
- I read with interest the article by Peter Kenyon reporting on the Acceptance of the first TBM for the Doha Metro. This follows the January 2014 article which headlines Herrenknecht sweeps Doha Metro Phase 1.
- The 'green giant' certainly has done well on this project and the article certainly sings its praises. I was interested to see Gunther quoted as saying after the first machine, three more were nearly finished in the Schwanau factory. Does this mean the remaining 11 machines are being delivered from the Herrenknecht Chinese factories?
- Following these two articles, on the 27 February, the TunnelTalk Editor's Desk Comment reads:
- "Owners and contractors.... are increasingly breaking with conventional wisdom.... of spreading.... risk between machine suppliers ....[and] make working with a single manufacturer an increasingly attractive option".
- Speaking as an independent, I cannot agree with the Comment. I have the highest regard for Herrenknecht, both as a company and for the high quality machines it produces, but it cannot be good for the industry, for the owners or for the contractors, when there is a monopoly of supply of such an important piece of equipment.
- The numbers of TBM suppliers has been slowly dwindling over the last 10 to 15 years, and now it is true that Herrenknecht is the leading supplier. Its market share must be extremely high, and we, as an industry, should be encouraging other suppliers to compete more vigorously, rather than suggesting or implying that a single supplier has benefits.
- I question the three reasons given in the TunnelTalk Comment.
-
"Economies of scale"
The suggestion that a single supplier, with no competition, will offer more economical machines is flawed. Whilst there are some aspects of the manufacturing process that a large quantity may produce higher efficiencies, it is a fact that every machine is slightly different, and every TBM is treated as a one-off. -
"Non-repetition in the design process"
This does not always follow as every contractor and every project has its own needs and requirements. A perfect example is in Hong Kong where two TBMs supplied by Herrenknecht for the same project and to work through basically the same ground, but for different contractors, are manufactured to two completely different designs. -
"Carefully phased rollout programmes"
I am not sure of the logic here, but every factory has a limit to the number of TBMs that can be produced at a single time. For a factory that becomes so busy, there is the reality of delivery schedules slipping and quality suffering. - Any industry that relies on a single supplier of important components will ultimately suffer. Without getting too political, it has to be true that competition is healthy for innovation, for quality and for price. Once it is seen that one supplier is so dominant and that contractors are always going to use the one dominant supplier, the potential competitors stop quoting for supply to that contractor. The feeling is "why waste our time quoting when we know we won't get an order?"
- The longer this dominant position goes on, the harder it is to break the situation.
- Both owners and contractors continually ask for track record of the manufacturers and as long as buyers stick with the same supplier, no-one else gets the chance to demonstrate its capability and build a track record. I know that there are some in the industry, amongst both contractors and owners, who are equally worried about this, but who do not have the courage to go out on a limb.
- As a single supplier becomes busier, and is not pressed by competitors, the quality of the supply is bound to deteriorate, both because of lack of alternative pressure and because the workplaces and factories become so busy that there is not time to keep up a high quality. Without wanting to make specific allegations, this is certainly true in my experience over the last two years with the TBMs that I have seen.
- In this respect, praise must be given to MMC-Gamuda on the KVMRT Metro in Kuala Lumpur, Malaysia. The JV purchased six machines of a very special design, and for which there was no possible competition, from Herrenknecht, but they refrained from putting all their eggs into one basket, and purchased two of the remaining four standard EPB machines from a Chinese supplier CREC-TBM (now known as CREG). And, it must be emphasised, the JV has not regretted its decision. The price competition achieved the desired result and the technical performances of the Chinese machines is not disappointing. It must be hoped that other buyers on other projects have the courage to follow this excellent example, and that CREG continue to be seen on other projects outside of China.
- There is more that can be said in this respect and in response to the TunnelTalk articles. For example, the emphasis on the German connection with Qatar seems out of place when the Red Line North contract is awarded to an Italian contractor, the Red Line South to a consortium that includes a French contractor, and the Green Line has a main Austrian contractor, but this letter is offered as a start of a discussion about competition, or lack of it, within the industry.
-
Best Regards,
Richard Lewis, YL Associates Limited, Hong Kong
Soft ground challenge for Doha EPBMs - TunnelTalk, February 2014
Herrenknecht sweeps Doha Metro Phase 1 - TunnelTalk, January 2014
Weekly Alert Editor's Desk Comment - TunnelTalk, 27 February 2014
Jury out on green infrastructure
Feb 2014
- Article references: DC Water scales back CSO tunnel plans - TunnelTalk, January 2014
- Dear TunnelTalk,
- I have followed DC sewer issues since 1968, although I am not a professional engineer. I was a stakeholder representing the Sierra Club during the formulation of the Long Term Control Plan back in 1999-2000 and am representing them in this current discussion.
- The DC Water proposal is just the beginning of a long process to request a modification to the Consent Decree governing the deadlines in the Long Term Control Plan - a request that must be approved by the EPA and the Department of Justice. While the proposal does a good job of outlining the costs of treating impervious surfaces in the District, there remains the question about how effective these measures will be and how quickly they can be implemented. DC Water concedes that green infrastructure on this scale has never been attempted and that there may be institutional barriers to solve, including long-term ownership and operation and maintenance issues.
- I am still digesting the 700+ pages of the report (Long Term Control Plan Modification for Green Infrastructure) but so far it is less than clear whether green infrastructure can substitute for the additional tunnel along the Georgetown waterfront (along the Potomac). On the Piney Branch (Rock Creek) tunnel, the overflows in that sewershed have much less volume and less duration and other structural changes may be cheaper and more effective and less impactful than a tunnel. But it is still early days on this and I am sure there will be robust discussion.
- DC Water will accept comments until March 14.
-
Regards,
Marchant Wentwort,
Wentworth Green Strategies, Washington, DC
Jan 2014
- Article references: Subsea tunnels for oilfield development - TunnelTalk, November 2013
- Dear TunnelTalk,
- I read with interest the article by EivindGrov and NTNU/Sintef colleagues about the continued interest in multiple TBM tunnels for personnel access and pipeline transport/production to-and-from off-shore petroleum locations, in their article Subsea tunnels for oilfield development.
- This of course shows some interesting developments in relation to the Troll-i-Fjell project that some of us worked on in Norway in the mid-1980s for the company Petromine. The stability of circular openings in some assumed weaker sedimentary rocks was the focus for NGI studies at that time.
-
Fig 1. Synthesized present world-record data for different sizes of TBMs using a log-log-log plot of penetration rate (PR) on the left axis only, advance rate (AR) in the remainder of plotted area, and time (T) as total hours
- The purpose for this letter is to show and discuss where TBM world records plot on the QTBM deceleration plotting routine, based on 1,000km of TBM case records using mostly open-gripper TBMs (Fig 1). In the same diagram, the predicted Grøv et al "283m/wk average" advance is plotted as a star, assuming this is the 'constant' rate of progress converted to m/hr. In relation to world record monthly rates, shown as two small circles on Fig 1, it would indeed appear to be "by far world record speed" and shows the need of continuing the deceleration out to performances seldom achieved (Fig 2).
- The world record performance at present is recorded as 16km in one year, providing a mean advance of 2m/hr. This is better than a mean of 283m/wk, so there is hope for this predicted performance (see the smiling face at 2m/hr mean for one year on Fig 1).
- The results in Fig 1 are based on data provided by The Robbins Company for all sizes of machines and including data for projects using TBMs supplied by other manufacturers. Day, week and month records (given in meters) have been converted to uniform m/hr rates by dividing assumed by the 24hr, 168hr and 720hr. Data from eight countries are represented chiefly from the USA and China. The record mean monthly data plots at advance rate (AR) = 1.7m/hr for the 3m to 6m TBM diameter class and at AR = 1.1m/hr for TBMs in the 6m to 10m diameter class. This is shown as the two small circles on Fig 1. The larger crossed-circle to the right is 54 weeks for 5.8km of the Svea Tunnel, achieved as the current drill-and-blast excavation record set by Norwegian contractor LNS. The tunnel was driven in coal-measure rocks and required significant shotcreting and bolting due to varied Q.
-
Fig 2. Trends from open-gripper case records representing 145 cases and approximately 1,000km of TBM tunneling(1)
- The five typical lines of performance in Fig 2. are the same as shown in Fig 1. There is some evidence, such as 56km of TBM tunnelling for the Guadarrama high speed railway tunnels in Spain, that very efficient double-shield operations could, at best, halve the general decelerations of data in Fig 2. The TBM world records plotted in Fig 1, however, using the same deceleration trend-lines, actually follow this general deceleration-with-time pattern, as do large EPB machines, but at much lower rates when operated in closed mode(1).
- The star in Fig 1 marks the presumed requirement for development of the sub-sea tunnels for oil-field production caverns as suggested by Grøv et al in their TunnelTalk article, if 283m/wk is indeed the intended mean. An estimated time of 13,095 hours or 77.7 weeks for one tunnel of 22km is of course, significantly less than the "generous" 210 weeks mentioned in the article for completion of a project that comprises drill-and-blast tunnelling of the access ramps and crystalline rock kilometers, the three 22km TBM tunnels, and excavation caverns etc.
- Grøv and his colleagues mention the results from the Fullprof software, applying the NTNU prognosis model estimate of 283m/wk, based on various feasible assumptions concerning cutter life and joint/bedding spacing. Rock mass strength is not mentioned but presumably is included, as in the QTBM prognosis method. As a weekly result this 283m/wk converts, by division with 7 days x 24hr, to a mean 1.68m/hour, which would indeed be a world record for a TBM in the 6m to 10m diameter range, if considered as a monthly average, or if continued for 22km which would imply 77.7 weeks, or 1.55 years, for completion, assuming 50 weeks of 7 day x 24hr production. Reaching the star in Fig 1 is indeed a significant goal.
- The authors Grøv et al, 2013, mention that "scheduling would require a TBM in each of the parallel tunnels to operate simultaneously and at high advance rates, working around the clock and for several years through challenging ground conditions". However, it is necessary to reconcile the presumed 77.7 weeks theoretical result with the "several years", as access to get the TBM in place is going to use a significant part of the predicted overall 210 weeks. It is indeed wise to assume that 283m/wk would not apply when there were challenging conditions.
-
Regards,
Dr Nick Barton
-
1. Barton, N. 2013. TBM prognoses for open-gripper and double-shield machines: challenges and solutions for weakness zones and water. FJELLSPRENGNINGS-TEKNIKK-BERGMEKANIKK-GEOTEKNIKK, Oslo, 21.1-21.17, Nov 2013.
2. Barton, N. 2000. TBM Tunnelling in Jointed and Faulted Rock. 173p. Balkema, Rotterdam.
Subsea tunnels for oilfield development - TunnelTalk, November 2013
Record drill+blast work in Norway - TunnelTalk, January 2009
Overly optimistic forecasts for PPP toll project proposals
July 2013
- Article references: Australia suffers toll concession failures - TunnelTalk, July 2013
- Dear TunnelTalk,
- From Brisbane, Australia: Easy, lower the tolls. More cars will then use toll tunnels, revenue will flow, and people will be happy to use the infrastructure. It may take a little longer to recoup the cost but you will have happy customers.
- From Greater Boston area, Australia: A good read. Sound assessments and risk profiling needs to be applied to these PPP projects. The goose does not always lay the golden egg.
- From Brisbane, Australia: Interesting reading. I have worked on the Airport Link in Brisbane both the design and construct contract and now on the operations and management side. It is truly a fantastic piece of infrastructure lead by some highly experienced Directors. ARUP/PBA really need to be held accountable and honestly, prosecuted for getting the projections so so so WRONG.
- From Brisbane, Australia: I understand this tactic, and by no means condone the methodology used by those to build these models, but we need to remember, false projections are easy to target, but if these organisations were not able to substantiate or, more likely, ‘sell’ these claims and projections initially, the financiers would not have supported the project and would not have had the opportunity to build these wonderful pieces of infrastructure.
-
See the original postings on our LinkedIn account.
Further comments will be added as they are received.
To add your comment, send us a message via our Feedback facility
Hands on experience to assist legal hearings
Dec 2012
- Article references: Expert witnesses and forensic consultants - TunnelTalk, Dec 2012
- Dear TunnelTalk,
- I believe hands on experience alongside academic expertise are invaluable when seeking help with arbitrations to assist the legal team to put forward a fully rounded case.
- Regards,
Ray Naughton, TBM Operator at Crossrail
'Imminent' and 'eminent' dangers
Dec 2012
- Article references: Tunnel ceiling collapse kills in Japan - TunnelTalk, Dec 2012
- Dear TunnelTalk,
- Apparently, in addition to failing bolts, some of them were missing. This is a perfect example of failure resulting from failing to consider 'imminent' and 'eminent' dangers.
- Regards,
Peter J. Tarkoy, Geotechnical and Underground Construction Consultant - From the Editor: An article to expand on this topic is to be published on TunnelTalk.
Being short-changed by 'local practice'
Oct 2012
-
Article references:
Rekindled NATM debate - SCL debate opens - TunnelTalk, Aug 2012
Defining NMT as part of the NATM SCL debate - TunnelTalk, Sept 2012
- Dear TunnelTalk,
- It seems that the opinion of the unnamed UK correspondent (see below) that: 'local practice should decide' on the method of tunnelling selected and applied to any project is 'sticking' as if recommended.
- Is this the best we have? I do not think so. If this were so then some good aspects of NATM or NMT or hybrids of both as appropriate to conditions, would be lost and time and cost would suffer in relation to the 'local practice'.
- Regards,
Nick Barton, International Consultant, Rock Engineering, Norway
Adding to NATM, SCL, NMT definitions
Sep 2012
-
Article references:
Rekindled NATM debate - SCL debate opens - TunnelTalk, Aug 2012
Defining NMT as part of the NATM SCL debate - TunnelTalk, Sept 2012
- Dear TunnelTalk,
- This may be a very naive view but I find the debate about the difference between SCL and NATM very confusing.
- I have always thought that the term SCL (Sprayed Concrete Lining) simply refers to the use of sprayed concrete to form a tunnel lining. There are of course numerous philosophies and design methods surrounding this technique but to me the term SCL is simply a term for a specific construction method.
- As for NATM, the way I have viewed that is the use of convergence confinement principles applied to a deep tunnel with the use of Sprayed Concrete Lining to enable the installation of a tunnel lining at the appropriate level of convergence. With a definition like this it becomes obvious why NATM is not applied to typical tunnelling in the UK (or at least urban tunnelling in the UK).
- Firstly one of the primary aims for urban tunnelling is to avoid excessive ground movements and this approach is fundamentally different to NATM where ground movement, up to a certain point, is actively encouraged to develop arching in the ground around the excavation.
- The depth of a typical NATM tunnel is also important because with large depths significant arching can be developed. For shallower tunnels the lack of overburden can inhibit the amount of arching of vertical loads that can occur.
- There are also issues related to ground behaviour; the magnitude of loads applied to the lining; and the required structural thickness of the lining that also prohibit a typical urban UK SCL tunnel being designed to pure NATM principals.
- Regarding the difference in philosophy between the Norwegian Method and NATM, I see these as just differences in philosophies. Local practise often dictates what is considered to be a good, safe, efficient, tunnel and what is considered poor construction practice. In different parts of the world, with different geologies, different histories, different construction constraints and different operational constraints, it is inevitable that different local construction practice applies. This seems to be particularly the case in rock engineering where you can find large differences in support in different regions. All too often one method is not necessarily better than any other. It is just different.
- Maybe in one region a thick shotcrete arch is a preferred solution, despite the fact that it is stiff and can attract extra loads. Elsewhere, for a similar tunnel, heavy bolting and a thin shotcrete shell might be the preferred solution for just as valid reasons. It is the skill in selecting from a suit of different design philosophies and tools to suit local geology, local construction practice and local constraints that separate an adequate design from a good design. No one philosophy is necessarily the right one for all tunnels.
-
UK contributor, name withheld by request
NMT added to the NATM-SCL-SEM debate
Sep 2012
-
Article reference: Rekindled NATM debate - SCL debate opens - TunnelTalk, Aug 2012
- Dear TunnelTalk,
- Congratulations on a masterful summing-up and reminder of earlier NATM contributions to UK tunnelling. It is nice to know that good quality shotcrete as 'single-shell' has now found its way into English tunnelling (Hindhead, Crossrail etc).
- Although the authors of three articles in T&T recently, who stimulated the TunnelTalk moderating comments, made reference to 'the Norwegians' and we could throw NMT into the pool of names, as this is a reflection of what has been going on in Norway/Sweden/Finland for many decades, first B+S(mr), then, after about the 1978-1983 transition, B+S(fr).
- NMT principles (single-shell) are not just applied in the granitic gneisses of the Fennoscandian bedrock, as many assume. There were, in fact, 50 rock types in just 212 cases in the 1974 Q-system development. Application of S(fr) in over consolidated London Clay via the Q-system logic was suggested in 1994. See pdf download: Updating the NATM
- Regards,
Nick Barton, International Consultant, Rock Engineering, Norway
NATM-SCL-SEM definitions and debate
Sep 2012
-
Article reference: Rekindled NATM debate - SCL debate opens - TunnelTalk, Aug 2012
- Dear TunnelTalk,
- I read with interest your supplement to David Hindle's article on NATM-SCL-SEM.
- While I sympathise with the general thrust of some of Dave's comments, especially the desire to avoid over-conservatism, many of his detailed points are misguided.
- For example, a lining sprayed in four passes - well, what happens in a traditional shotcrete supported lining? An initial sealing layer, a first layer of mesh, the main shotcrete pass, a second layer of mesh, a final shotcrete pass and then the secondary or final shotcrete or in-situ concrete lining inside. Is not that four passes? Except of course, because bars and lattice girders are used, a client like LUL would not accept the primary shotcrete passes as part of the permanent works. That itself is a point Dave has completely missed in his critique. The drive to use fibres in a (largely) unreinforced lining is partly to assuage the concerns of clients who doubt the durability of a bar reinforced primary lining.
- There are numerous points in Dave's comments on the Crossrail design which are inaccurate and, had he known or spent the time to find out the constraints, he would understand why it is how it looks. I daresay that it could be improved and I believe some in the Crossrail SCL design team have sent a detailed response to the original article published in T&T, elaborating on the misguided nature of the comments.
- Perhaps I misunderstood the thrust of the TunnelTalk article but at one point it seemed to imply that, after Channel Tunnel, UK designers had pinned a badge to themselves as SCL experts without bothering to try to understand the method. A few people in Mott MacDonald, for example, might take issue with that suggestion, given their own contribution to the Channel Tunnel's SCL design alongside ILF of Austria, their subsequent work on Roundhill (there are other contemporary SCL road tunnels too, including Pen-y-Clip) and the SCL trials at Heathrow, as well as Red Cross Way, the SCL trial tunnel for the Jubilee Line Extension of the London Underground near London Bridge, and the major investment in SCL R&D thereafter, including a series of PhDs and joint research projects, such as Brite Euram. It is worth noting that UK engineers have played a role in innovation of SCL tunnelling in recent years and in fact, in some cases, lead a path that the Austrians and others have followed.
-
Dave did ask for a definition and some explanation on the role of monitoring (in soft ground applications). If it helps, here is my definition:
"An SCL tunnel is a tunnel with a Sprayed Concrete Lining. The Sprayed Concrete Lining interacts with the ground and, through the choice of excavation sequence, this interaction can be optimized to minimize the loads on the ground support. Monitoring is required for 'performance verification', to ensure that the tunnel is performing within the limits required by the design (given natural variations, for example, in advance rates and ground conditions), to determine when certain contingency measures are needed (such as temporary inverts)." - Regards,
Alun Thomas, BA PhD CEng MICE,
Author, Sprayed Concrete Lined Tunnels
Tunnels Head of Department, Ramboll, Denmark
Sprayed Concrete Lined Tunnels - TunnelTalk, Books & Reports
Personal friends and character appreciations
Sep 2012
-
Article reference: Rekindled NATM debate - SCL debate opens - TunnelTalk, Aug 2012
- Dear TunnelTalk,
-
I think that you have done Dave an injustice.
"For those who know Dave Hindle personally", you missed out a cantankerous Lancastrian who does not wear fools gladly. - Regards,
Phil Richardson, Natural Cement Distribution Ltd, UK
Personal friend and colleague
High speed, early strength shotcretes
June 2012
- We at Natural Cement Distribution in the UK have been producing fast setting, fast curing, high early strength, waterproof shotcretes since 1996 that will out-preform the product described in the article War on terror heralds shotcrete breakthrough. We have shotcretes that are not a mixture of many additives, will not poison future generations, and are better for the environment than the product describe. May I suggest that you look at Shotcrete 513 in the Shotcrete section of our website to know more.
- Regards,
Phil Richardson, Natural Cement Distribution Ltd, UK
War on terror heralds shotcrete breakthrough - TunnelTalk, June 2012
Fatal ring-build accident at Lake Mead
June 2012
- Detail is not provided but from the read it seems the thrust ring was retracted to be ready for the next set. If so, the TBM was not moving forward so the tapered segment would not have been pulled.
- Might the taper have been the source of the movement? The exterior pressures were reported to be quite high. The resulting squeeze might have been sufficient (depending on joint friction) to cause the movement. Sort of like squeezing a watermelon seed in your fingers.
- Carl Linden, P.E., Senior Construction Manager, URS Corporation (Los Angeles office)
Fatal ring-build accident at Lake Mead - TunnelTalk, June 2012
Sochi winning on the Olympics alpine route
February 2012
-
Further to the story:
Two of the TBMs used on the project are in fact refurbished Robbins TBMs. The 10m double-shield machine that excavated the 4,564m rail tunnel for the Tunnel System 3 started its working life as a new Robbins machine as did the 6.2m TBM used for the3,197m System 3 service tunnel. Once refurbished and delivered to the project by Lovat-SELI, Robbins was contracted to supply service and technical support in the mobilization, operation and maintenance of the equipment. This included the supply of critical spare parts for continual TBM operation.
Sochi winning on the Olympics alpine route - TunnelTalk, Feb 2012
Tunnel death leads to $55,000 fine
October 2011
- In reading this item the level of fine seems relatively low considering the loss of life, which is tragic under any circumstances. One wonders if the contractor knew fine levels were low and therefore permitted a superficial culture on safety and operation to exist.
- Charles W. Egerton
Tunnel death leads to $55,000 fine - TunnelTalk, Oct 2011
Allowable volume loss calculations
September 2010
- In reference to maximum allowable volume losses as discussed in the Crossrail settlement control measures article.
- When I worked in the UK I always wondered how to get along with the historical progression of allowable volume losses. According to the British Standard some companies told me that they do some calculations about volume losses in every phase of design, let's say C then D, E, and by F, and for most design-build criteria as well, they go from 3.5% to 2.5% then 2% and arrive later at 1.5% or 1% in Stage F. Good practice would be to use the same allowable volume loss criteria during all stages of design and invoice the client accordingly. Instead of using the actual allowable volume loss from the beginning, the actual rate they will use for the final design turns up in stage F. In this way the design hangs on a rate that for some tunnel shapes will not be accepted in design stage C because the maximum allowable volume loss is too high! If they would use the actual 1% rate from the start it would be fine.
- Further this calculation is very conservative for the actual volume of the tunnel shape x percentage of the actual progress, or let us say the indicator time. How long will the excavation and support go on? Also, the method of excavation, whether by TBM or NATM (SCL), is not indicated in this calculation. So it is just a total guess and will never reach true accuracy.
- Tunnelling in London has been going on since Brunel's Thames Tunnel in 1825 and it is only now, in the last few years, that there is a real start to calculate this issue. By now we should be able to know what is feasible or what is not doable. With regard to applying the reduced assumption of 1% face loss on Crossrail, has someone just woken up and started thinking about this? Let us hope for better news from the island.
- Robert
Crossrail geotechnical series - 3 - Settlement control measures - TunnelTalk, Aug 2010
Dublin Port Tunnel's successful DRB panel
August 2010
- We have learned the composition of the DRB that facilitated settlement of outstanding claims between the owner and the design-build contractor of the Dublin Port Tunnel in Ireland. The three-member panel comprised:
- Peter Chapman, Chair (UK), Brian Eggleston (UK), and Dr Terry Mellors (UK).
- Contributing to the debate about the selection of a successful DRB, we can confirm that all three members of the panel are engineers, with one also a qualified barrister.
- Chapman is an engineer, as well as a qualified UK Solicitor, and a past President of the DRB Foundation (2004-2006). He is a well-respected member on dispute resolution, mediation and arbitration panels.
- Eggleston is an engineer and involved in dispute resolution through mediation and arbitration. He is regarded as the expert on the application of NEC3 Contracts and has written several books on the subject.
- Mellors has a degree in civil engineering, an MSc in Engineering Geology and a PhD in Engineering Geology, all from Imperial College London, and has extensive experience as a design consulting engineer. He is a past Chairman of the British Tunnelling Society (BTS) (1999-2001) and was Joint-Chairman of the Working Group that produced The Joint Code of Practice for Risk Management of Tunnel Works in the UK, prepared jointly by the BTS and the Association of British Insurers as well as a primary author of the international version.
- Further discussion on the topic reveals that most commentators agree that DRBs need an engineering pragmatism to succeed, and a agree concern that DRBs in both Europe and in the United States are tending towards appointing more lawyers. Another point of concern expressed was that members on DRBs in the USA are becoming partisan, adopting a position of protecting the Party that has appointed them, which is contrary to the understanding that appointees are meant to be independent and strictly non-partisan.
- The debate continues.
DRB scores success in Dublin - TunnelTalk, Aug 2010
Advocating for more DRBs in Canada - TunnelTalk, Aug 2010
Dublin Port Tunnel settles claims disputes - TunnelTalk, Aug 2010
DRBs in North America - knowing and playing by the rules - TunnelTalk, Aug 2008
Enhancing the success of DRBs - TunnelTalk, Oct 2008
Safety first!
August 2010
- We are grateful to Jim Hinze, Senior Safety Engineer with Cal-OSHA, who pointed out that a photo we published last week on the Caldecott fourth bore start of excavation included evidence of safety violations.
-
- Visitors watching the launch of the roadheader at the start of the Caldecott highway tunnel fourth bore excavation in Northern California are photographed not wearing a hard hat. As Hinze said: "Down in a deep portal cut with all kinds of possible overhead hazards is no place to be without a hard hat!"
- Remember guys, accidents are not selective. A hard hat is as essential as steel-toed boots, ear defenders, goggles and an acute awareness of your surroundings when visiting any job site.
- We have removed the photo from the Digging begins at Caldecott article and post it here as a reminder that safety is always first.
- Thanks to Jim Hinze for making the point once again.
Learning from mistakes
July 2010
- Interesting report on collapses!
- One could add a long list of other collapses (NATM, TBM or not), like Glendoe and Gigel Gibe II etc.
- I also agree with you: one should learn from successes not mistakes. Confucius says: "Experience is like a lantern in your back. It lights only the already traveled path!"
- If you look at the top sports trainers, they never tell of the mistakes you've made. Only of what you've done well and to improve on it!
-
Carlo Bretz
Switzerland
Discussion Forum - Symptoms of the collapse syndrome - TunnelTalk, July 2010
Rock falls shut down Glendoe power plant - TunnelTalk, Aug 2009
Glendoe rockfalls more serious than initial fears - TunnelTalk, Oct 2009
Recovery contract for failed headrace at Glendoe - TunnelTalk, Feb 2010
Collapse of headrace tunnel after grand opening - TunnelTalk, Feb 2010
Repair of limited collapse in Ethiopia - TunnelTalk, Mar 2010
Fundamental contributors to industry problems
July 2010
- Big problems for the industry, in my personal opinion, are price dumping, budget cutting, assssnd time saving - and that in a field of highest safety requirements. Tunnelling industry has sometime not too much respect for its own achievements, and should not let advocates make the business. Most importantly on the negative side is talking badly about competition and badly about the industry itself.
- A reader in Germany
Discussion Forum - Symptoms of the collapse syndrome - TunnelTalk, July 2010
Adding to the symptoms of the collapse syndrome
July 2010
- You touch on the fact that supervision at night tends to be lessened and that the construction team is often the B team. It has been observed on many occasions that junior newly qualified engineers on the night shift are placed with an experienced team headed by a foreman or supervisor who is usually older and in theory should have more experience. Whilst many young engineers see things being done that they consider as being wrong, they cannot comment for the reason that they will be referred to as being 'wet behind the ears' and by being told that "this is the way it has to be done". Another syndrome that takes place on the night shift is that the absence of watching eyes results in the cutting of corners.
- Any senior engineer on the night shift will be working alone and will have been left with a list of functions related to sorting out the back-up infrastructure and completing unfinished paper work.
-
There are two things that should be dispensed with:
a) Advance rate bonuses, which have the effect of making it almost inevitable that requirements in other areas will be forgotten. An example is quiet simply blocked annular grouting pipes resulting in not being able to keep grouting at the same speed as TBM advance, but carrying on with excavation regardless.
b) 12 hour shift patterns, which lead to workers, in an already stressed environment, being over tired and taking their minds off the ball. Cutting down shift times is an area that meets with considerable hostility. It is time for projects to be managed by the engineers (managers) who must face the flack of any incident, rather than finding someone lower down the chain of command to take the blame. - You also mention the failure in Cairo, in which you mention that bolts were "forgotten". Were they forgotten or did someone come to the conclusion that bolts are to be removed later, so why put them in the first place! People forget the rotational forces applied by the TBM. Cutterhead torque has to go somewhere. As Newton's Third Law that states: "For every action there is an equal and opposite reaction." I have observed personally segment joints opening up as a result of cutterhead torque. In some instances this has sheared both dowels and bolts and opening up the longitudinal segment joints.
- Charles W. Egerton
North Ayrshire, UK
Discussion Forum - Symptoms of the collapse syndrome - TunnelTalk, July 2010
Learn young and from small mistakes is the key
July 2010
- I think you might want to modify slightly your comments on learning from failures to include the following:
- All of us should be lucky enough to start in our 20s learning from our own small failures. More is learned from bad jobs than good jobs. Perhaps as important is to pay attention to details of mistakes that "almost" or "could have" resulted in very serious consequences.
- I believe that most of the serious cave ins you write about would not have occurred had a couple of the people in charge (including designers, owners, engineers, contractors, etc) had more 'failure' experiences in their 20s. Unfortunately that kind of good experience is less common now and perhaps the reason why we are seeing more of these unnecessary problems.
- Thank you for writing about this topic in your editorials. It needs more knowledgeable discussion.
- A reader in the USA
Discussion Forum - Symptoms of the collapse syndrome - TunnelTalk, July 2010
Filling in the list of giant TBMs
June 2010
- Thanks to the readers who let us know of the missing entry on our list of mega +14m diameter TBM projects. The 14.2m diameter Herrenknecht Mixshield used to excavate the 4th Elbe River Road Tunnel in Hamburg in 2000 is added to the list along with the two highway tunnels in Moscow that the machine went on to excavate. Also added is the 14.4m diameter Robbins open main-beam gripper machine working on the hydro scheme water diversion tunnel at Niagara in Canada.
- Good to know you are paying attention.
Taking mega TBMs to greater diameters - TunnelTalk, June 2010
Natural cement contributes to waterproofing of the Hindhead project
March 2010
-
- In reference to the spray-on waterproofing of the Hindhead tunnel, I would wish to advise of some of further information.Among several methods tried to prevent and divert areas of water ingress ahead of application of the spray-on membrane, one the most effect ways was application of a natural cement based shotcrete call Shotcrete 513. Many tonnes of this material were used to stop the water ingress and allow the application of the Masterseal. the day joints were not always water proof and that by over spraying afterwards with our Shotcrete 513 it stopped the ingress of water allowing the application of the Masterseal which cannot be applied to areas of tunnels where there is an ingress of water.
- Regards,
Phil Richardson, Natural Cement Distribution Ltd, UK - TunnelTalk: While the text doesn't state the case specifically, it does address the "permeability specification of 1 x 10-12m/s for the primary shotcrete provides a waterproofing barrier of quality itself". The natural cement based product would have contributed to achieving that quality.
- Phil Richardson: The problem was that the day joints were not always waterproof and that by over spraying afterwards with our Shotcrete 513 it stopped the ingress of water allowing the application of the Masterseal.
UK applies spray-on waterproofing – TunnelTalk, March 2010
Various support products but spray-on is the waterproofing system throughout
March 2010
- The natural cement product was used but as one of a number of measures that were adopted for the purpose of dealing with areas of water ingress. The project adopted a methodology of having a suite of solutions available to the construction team allowing them to respond immediately to the conditions that presented themselves. We used it to cover damp blooms or to cover strips of water channeling Delta membrane. There are a number of products used to assist in the application and performance of the Masterseal. There are no areas of the mined section of the tunnel where other products are operating instead of the Masterseal.
- Roger Bridge,Tunnel Manager, Balfour Beatty,Hindhead Project
UK applies spray-on waterproofing – TunnelTalk, March 2010
Providing useful information
March 2010
- Dear TunnelTalk,
- In reference to the Hindhead spray-on waterproofing article, you published all the right info - very useful. All too often key productivity and other data that lets the reader estimate costs are omitted from articles. Observations of crew size, equipment, and time to perform, including work schedule, go a long way to letting readers conclude for themselves how cost effective is the process.
-
With thanks,
John M. Stolz, PE, Principal,
Jacobs Associates,
San Francisco, California
- TunnelTalk: Thank you. Reporting information for advancing the art and science of successful tunnel and underground space excavation is the mission.
UK applies spray-on waterproofing – TunnelTalk, March 2010
NATM more cost effective than TBMs for Santiago Metro
March 2010
-
- Last week, when reporting on the consequences of the massive 8.8 earthquake on underground structures in Santiago, Chile, we included by mistake reference to TBM driven tunnels for the Metro system. The error was pointed out to us by a reader and has since been corrected. All underground sections of the Metro de Santiago are either cut-and-cover structures in earlier times, or NATM excavations for stations and running tunnels since the mid-1990s.
- Reprint of articles from our archive explores the introduction and development of the NATM concept as a highly cost effective method of metro construction in Santiago and and refers to the results of a study that confirmed the advantages of NATM over the TBM alternative for construction of metro running tunnels in the Chilean capital.
Santiago goes underground with NATM – TunnelTalk, April 2003
Optimised NATM designs for Santiago Metro – TunnelTalk, April 2003
Santiago Metro withstands massive earthquake – TunnelTalk, March 2010
Inclined TBM drives and a rival TBM decline record holder
February 2010
-
11m diameter drive on a 30° decline
- Last week we published news of a new 8.03m diameter Aker Wirth TBM claiming to drive the world's largest inclined TBM tunnel. On order by a Swiss contractor, the TBM will drive a 4km long, 24% inclined access tunnel for a hydropower plant expansion project in Switzerland.
- We have since had news from Lovat claiming a larger, steep gradient TBM drive although this time on a decline rather than an incline. An 11m diameter mixed ground machine was used to excavate a 150m long x 30° declined escalator access shaft for the Moscow Metro system in Russia. The first of many planned escalator access drives for the Metro was completed in January 2009 and the machine now awaits start of the second drive, once funding allows.
-
LOVAT EPBM ready to head to Moscow
- From our Archive we publish an article about another Lovat TBM incline of 30° completed in 1997 as part of an emergency to finish the top 400m of the steep penstock for the Cleuson-Dixence hydro project in Switzerland and not a long way from where the new Aker Wirth TBM will work on its steep incline for the Linth-Limmern power plant expansion project in the Canton of Glarus, south of Zurich.
- While there is a difference direction, an incline and a decline are both working off grade and a decline can be considered the more challenging and potentially dangerous. There have been many steel inclined TBM tunnel drives but we know of only the Lovat Moscow Metro system large diameter TBM decline drive. If you know of other incline or decline TBM drives, do let us know and we will keep the record.
Top down TBM escalator drives - TunnelTalk, February 2009
Steep TBM drive for Swiss hydro scheme - TunnelTalk, February 2010
Steep incline drive saves critical deadline - TunnelTalk, April 1997
EPB and slurry machine mix up
October, 2009
A reader has informed us of an error in the our report about the Cairo Metro tunnel sinkhole article. In it we mentioned other TBM metro tunnel collapses and wrongly stated that it was a Mixshield working on the Porto metro project in Portugal. It was in fact an EPB machine that was working on the project and on which a tunnel sinkhole caused a building to collapse and claimed the live of one victim.
Cairo Metro TBM tunnel collapse – TunnelTalk, September 2009
Ring beam erector still there at Jinping
October 5, 2009
TunnelTalk stated recently and incorrectly in the London conference report, that the ring beam erector on the 12.4m diameter Robbins TBM working on the Jinping project in China had been removed. Lok Home, President of The Robbins Company, has corrected the information saying that in fact Robbins had wanted to remove the ring erector as part of the rock-support installation equipment modifications but that the client insisted that it be rebuilt and retained. That was done and the ring erector is still on the machine, with the introduction of the man-carrier booms making it easier to access the large diameter span and install the ring beams. Home remains of the opinion however, that ring beams have no place as rock support elements in tunnels of 8m in diameter or more and that NATM support elements of rockbolts, mesh and shotcrete are more effective and easier to apply on such large diameter rock-TBM tunnels.
Conference report: London's eye on the underground scene – TunnelTalk, October 2009
Onsite build for giant Jinping-II TBM – TunnelTalk, October 2008
Safety regulations grow from disaster
September 17, 2009
Kudos to Tunnel Talk and the author of the Hawk's Nest Tunnel Tragedy Article. Modern miners often forget how many lives were lost during the dark times of lax and/or criminal neglect regarding environmental and workplace safety in underground excavations.
Sincerely,
Gordon Revey, P.Eng.
Hawk's Nest Tunnel tragedy – TunnelTalk, September 2009
Contract termination - the expensive no-return option
April 2009
On a recent e-alert, the “From the Editor's Desk” message asked: "How do relations between Owner and Contractor become so intractable when contracts get into trouble and end up in termination?" It went on to ask: "Where was the dispute resolution process? Where was the co-operation to work through a difficult situation? Is termination the only solution when relations breakdown? Is the cost of rebid always fully appreciated by the boards of public owners ahead of termination?"
With respect to some of the questions about this topic, one of the ways these things fall apart is when the parties take the back-and-forth rhetoric personally. Once you begin to think in terms of “making a point”, and lose the focus on “how do I finish the job”, all hell can break loose. I’ve seen it happen, especially with big egos on either (or both) sides of the table.
William W. Edgerton, P.E.
Principle and President,
Jacobs Associates
San Francisco, California
TunnelTalk: Would it not serve the public and the project better to include a clause in the contract that senior management on both sides be turned out and new negotiators brought in before failure of discussions heads towards contract termination? There will be contract terminations in the future but the damage, the delay, and the cost make it no easy or simple solution. Recent rebid of the terminated Seymour-Capilano project in Vancouver is double the original contract price and the same was true for rebid of the DRO-2 outfall tunnel project in Detroit, which has been recently terminated for the second time due to financial constraints. The appointment and operating procedures of DRBs (Dispute Review or Resolution Boards) and methods of enhancing their potential for success has also been the topic of Discussion Forum.
Seymour-Capilano restart comes at a high price – TunnelTalk, April 2009
Detroit outfall contract terminated – TunnelTalk, April 2009
DRBs - knowing and playing by the rules – TunnelTalk, August 2008
Enhancing the success of DRBs – TunnelTalk, October 2008
Detroit water tunnel projects crippled
April 2009
Anonymous
Shouldn't the alert headline this week read; "Detroit is incompetent in more areas than just the motor industry"? They seem to be able to destroy any decent contract from any position. I cannot imagine the ground conditions are so overwhelmingly bad that it is impossible to mine. Amazing!
Detroit outfall contract terminated – TunnelTalk, April 2009
Funding crisis cripples Detroit tunnel projects – TunnelTalk, April 2009
Brightwater under pressure
February 2009
Lionel Suquet, Project Manager for the Vinci/Parsons RCI/Frontier-Kemper JV
“There have been more than 250 hyperbaric man-entry interventions at up to 4.8 bar pressure during the 12,500ft (3,800m) of tunnel completed to date by the two Herrenknecht slurry Mixshields being used on our Central Tunnel contract for the project. This allows only 45 minutes of work in the air by our compressed air maintenance crews with three hours in decompression. There are up to six three-member maintenance crews available in a 24-hour period and it is taking up to three times 45 minutes to change just one cutter.”
Name withheld
Investigation reveals that factory testing of the integral airlocks delayed delivery of West Tunnel contract’s TBM to site. Contract documents set rigorous pressure loss vs time specifications that had to be met before acceptance and ex-works delivery of the machine.
Name withheld
The remote camera sent in to check cutters on the LOVAT EPBM working on the West Tunnel contract, confirmed them as “like new” after 700 rings (1.5km) of tunnel excavated. This is a positive situation in the abrasive glacial conditions of the alignment.
Brightwater under pressure – TunnelTalk, February 2009
In response to the article, 'AMR India Project'
January, 2009
It seems the Alimineti Madhava Reddy (AMR) Project with it 43km long irrigation tunnel to deliver water from the Srisailem Reservoir to a vast drought-prone area of farmland and villages in the central state of Andhra Pradesh in India has a long history. Feedback and anecdotes from readers in the UK tell of an attempt in the 1970/80s to design and build the tunnel.
Let us know if you recall earlier attempts to develop this benchmark project.
Maurice Gooderham, Retired, Formerly Director of Thyssen (GB) in the UK, Surrey, UK
“I read with interest the Srisailem article. In 1986 Thyssen GB was interested in the project with designers Howard Humpreys. The original documents noted that the tunnel route traverses "an area inhabited by wild and ferocious beasts”. I assume the risk of a survey team being eaten by tigers was avoided by the current availability and use of GPS.
Maurice Gooderham, Retired
Formerly Director of Thyssen (GB) in the UK
Surrey, UK
David Hindle, Tunnelling Engineer, Director, OTB Consultants, London, UK
“Believe it or not, this is the project that first got me working with Maurice Gooderham back in 1978. I was a grubby junior tunnelling engineer working for Howard Humpreys, fresh out of the mines of Africa and the burning deserts of Oman.
We got an enquiry from the Government of Andrah Pradesh to bid for the project in partnership with a suitable international tunnelling contractor. I ring Maurice and he suggested we should meet that very afternoon to discuss the options.
Howard Humpreys (now Jacobs Engineering) was based in Leatherhead, Surrey in England and the Thyssen’ offices were in Llanelli in Wales. It is a fair old way between the two and after starting at 11am and travelling on several connecting trains I arrived hot and bothered some time after 6pm, thinking I would be too late and they would have all gone home. Not a bit of it. I was ushered into Maurice’s grand office and money changed hands between Maurice and a colleague who had laid a bet on whether I would get there that day. "Never mind lad," said Maurice. "It’s not urgent we can talk about it tomorrow.” It marked the beginning of a beautiful friendship.
The Srisailem job died a death at that time and has been resurrected several times over the years - a bit like other major projects, including Crossrail in London, except that it is being built at last.
David Hindle, Tunnelling Engineer
Director, OTB Consultants
London, UK
In response to the article, 'Rebid Reprieve for Seymour-Capilano'
January, 2009
John Penner, Manager, Contracts, Bilfinger Berger Canada Ltd.
Dear TunnelTalk,
In the article Al Johnson, Regional Director for Construction, WorkSafeBC, discusses shutting down work operations on the Seymour Capilano project and comments that he could not recall if workers exercised their right to refuse to work.
Bilfinger Berger notes that his statements are misleading and inaccurate.
First, on January 22, 2008, WorkSafe BC issued orders to Metro Vancouver and Bilfinger Berger Canada and verbally directed and required the delivery of an investigation report and a safe design before any work was to proceed. To date, neither of the orders has been rescinded. In addition, WorkSafe BC has not approved any plans to resume tunneling or varied its directives to allow any tunneling.
Second, the three unions representing workers on the project all agreed with Bilfinger Berger's decision to stop tunneling after workers were injured. In a May 30, 2008 letter to Metro Vancouver's Greater Vancouver Water District, the three union leaders stated: "After our members were injured and exposed to unsafe conditions at the site, Bilfinger Berger made the correct decision to temporarily suspend the work pending a review and analysis of the rock behavior."
The safety of Bilfinger Berger workers is the company's No. 1 priority. The fact is representative worker unions and their workers are fully onside with Bilfinger Berger's position: They agree that working conditions were not safe; they agree that suspending work was the correct decision; and they have asked Metro Vancouver to review its decision to terminate Bilfinger Berger's contract.
Yours sincerely,
John Penner
Manager, Contracts
Bilfinger Berger Canada Ltd.
California fixes high-speed rail route
July, 2008
-
Name withheld
I am working on a study for upgrading a rail system for the east coast of the United States. This is new investment to increase rail capacity to accommodate separate intercity, commuter and freight services. These are co-mingled in most places at the moment and separation is essential ahead of projected doubling of freight rail in the region by 2030. Rail must relieve highways.
-
Alameda Corridor LA
- TunnelTalk: Separating freight from passenger traffic is the conundrum the world over. Japan and Europe bit the bullet early with construction of d edicated high-speed lines for passengers but the needs of the freight traffic have really come into their own and especially with the dramatic rise in fuel prices for truck t ransportation. The Swiss baseline rail tunnels were promoted as the green alternative to trucks that were killing off the trees through the mountains with acid rain - remember that? - but they will be ahead of the game now on the more urgent need to address fuel prices. Discussions on all these topics - and particularly about the cost of building passenger train tunnels as opposed to freight train tunnels - was very interesting at the project in Austria. It seems to be the beginning of a sea change in high-speed rail thinking in Europe. Another issue that the US is yet to address seriously is the issue of grade separations to be rid of the many disruptive and dangerous level crossings on their networks.
-
Alameda Corridor map
- Much of the $950 million set aside by the California HSR Authority for service upgrades on existing feeder lines is to construct the over and under passes to eliminate level crossings. The $2.4 billion Alameda rail corridor linking the ports of Los Angeles and Long Beach to East Los Angeles rail yards was designed in large part t o eliminate traffic congestion at road grade crossings. http://www.acta.org Some 30 roads were elevated above the tracks while more than 200 other grade crossings were elimin ated depressing the two express rail tracks in a 10m deep cut for a distance of more than 15km.
-
Name withheld
Grade separations to avoid level crossing are the required course for speeds in excess of 160kph but the bigger issue is more tracks entirely for capacity for both freight and passengers and still not have the footprint of big highways.
Australia’s highway tunnel pain continues
February, 2007
City Link Tunnel
David Baxter, CPEng. FICE; MIE(Aust) Melbourne, Victoria Australia
Recent events on Melbourne’s City Link highway tunnel in Australia underscore FIDIC’s view that the Silver Form Conditions of Contract (EPC/Turnkey Projects) are not suitable for underground work (reference: Introduction to First Edition).
In essence Australia’s design-build contracts adopt a Silver Form approach by having detailed performance specifications, putting all the risk on the contractor including ground conditions and so-called reference material and workmanship specifications as provided by the client’s consultant, which the contractor is free to adopt or write it’s own.
In January 2007, Transurban, the owner/operator of the City Link Burnley Tunnel issued a statement saying it plans to sue the contractor, Transfield-Obayshi JV, because the tunnel was unlikely to last its’ forecast 100-year lifespan because its’ cast concrete walls were too thin. City Link has been plagued with problems on the tunnel since design and construction began. Many of the issues have been reported in the media. A settlement of the claims between all parties back in 2001 was mediated behind closed doors, losing a prime opportunity to improve industry practices.
Recent reports in the Australian media refer to walls not being built to specification. This implies a breakdown of the contractor's quality assurance system leading to a construction defect - not a design error. The self-certification process, intended to certify construction integrity without the need for independent checking, was relied upon by the client to indicate that construction quality was adequate.
A newspaper article in late January alleges claims by the independent assessor that he was pressured to approve the tunnel for opening. If this was so, and no denial has been published so far, the Melbourne public should be somewhat alarmed that the check to avoid faulty design and/or construction has been subverted.
There have been claims in the industry that the City Link’s Burnley Tunnel situation is a worse indictment of the industry’s ills than the circumstances that led to the Heathrow Express station cavern collapse in London in 1994 (Heathrow failures highlight NATM misunderstandings). It certainly has similarities due to inadequate construction standards. Reliance on design-build procurement and self-certification procedures on these projects certainly vindicate FIDIC’s reservations about the use of the Silver Form of contract for underground works.
Responsibility: Why We Don't "Just Do It"
February, 2007
William Edgerton, Jacobs Associates, San Francisco, USA
As I read the article about the Lane Cove tunnel collapse, it occurs to me that we need to have a better understanding of our responsibility for safety of both workers and the general public. I wondered how we as engineers, and indeed as an industry, are able to bear the burden of responsibility that we should feel for the performance of the projects we design. And it occurred to me that perhaps we bear it by not keeping it in the forefront of our minds as much as we should. A failure should always remind us to review our practices, because a failure offers more opportunities to learn than a success ever will. Success sometimes happens "in spite" of our efforts; failures always happen because of things we did wrong. In this respect, our projects are a bit like Tolstoy’s view of families as expressed in Anna Karenina: “Happy families are all alike; every unhappy family is unhappy in its own way.” We each fail to assume our responsibilities in unique ways.
Each party in an underground project has a set of responsibilities when it comes to safety. Owners set the stage for a safe project and serve as the behavioral model for all of the other team members. Not only do they approve the concept, but they significantly influence the safe design, construction, and operation of the facility by: (1) establishing realistic schedules and budgets for investigations, design, procurement, construction, and operational testing, (2) requiring detailed occupational health and safety plans to be implemented during construction, and most importantly, (3) insisting upon inter-team communication protocols that enable all project participants to be made aware of previously-collected information that can influence their judgment and affect their own responsibilities. Designers must recognize all potential risks, and present to the clients recommendations for ways to manage them. It is incumbent upon the designer to identify and convince the client of the importance to fund appropriate site investigations, geotechnical and otherwise. Not only must we establish design and material parameters for the final facility that enable it to perform to the intended criteria, but we must perform the detailed analysis, including necessary modeling, to indicate the ground and structure behavior during construction, and to ensure that the work can be constructed without damage or injury to third parties. And most importantly, we must evaluate the actual ground conditions during construction to verify that they agree with the assumptions made during the design process, and notify our client in the event that they do not. On design-build projects, in serving our contractor clients, we are obligated to assist in developing economical means and methods of excavation support, but in so doing we must never compromise our obligations to public safety that result from our engineering licenses. Contractors have an obligation to their workers to provide a safe work place. To do this they must plan the work in advance, establish appropriate work methods to accomplish it, employ workers who are competent for the work anticipated and have a safety focus, provide suitable training, and supervise the day-to-day activities such that workplace safety is paramount in everyone’s mind. Many construction contracts make the contractor responsible for the design of initial excavation support in portals, shafts, and tunnels. As a result the contractor must employ and direct suitably licensed professionals to perform the necessary analysis in order to ensure safety of the resulting underground openings.
Though I've outlined these responsibilities separately, owners, designers, and contractors don't fulfill their responsibilities in isolation. The responsibilities of one party overlap with those of another, and the actions of one party cause reactions and impacts. Yet, the actions that need to be taken are themselves relatively clear. So why don't we take them?
Sometimes, the parties are ignorant of their responsibilities. An owner may be building a project of a type they haven't built before, or a designer or contractor may be working with material that hasn't been used on similar projects. Other times, we may know of a responsibility or opportunity to be more thorough, and simply ignore it. Or, we may be so focused on a particular goal that we lose sight of some of the other aspects of the project that require our attention and planning. We have to guard against each of these tendencies, in ourselves and in the people with whom we collaborate. In a true partnership, the parties help bring each other into balance to achieve success. Only when we recognize the ways in which we fail to assume our responsibilities can we begin to correct our habits and build projects that are successful because of us, not in spite of us.
CERN's success, an underground triumph
September, 2008
Trans-border SSC
Clair Murdock, Heavy Construction Consultant, Ottawa, Canada
Even more distressing than collapse of the SSC in mid-tunnelling were the raw politics that sited it in Texas; not across the Canada-USA border near Malone, NY. Better rock, cheap electricity from Canada, and Canadian (and other international) funding possibilities ignored. The trans-border site would have been seen as international, not as Domestic, and some of the funding since committed to CERN would have supported the project. A compounded tragedy, with the best and brightest scientists going to CERN, not Montreal.